製造業にとって、品質不良は大きな課題です。不良品は社内での手戻り増加だけでなく、顧客満足度の低下、さらには市場に出回ってしまうと重大な事故が起きてしまう危険性もあります。
本記事では、品質不良、不良率や目標数値の目安を解説します。さらに、不良品の原因究明の考え方や対策、再発防止や未然防止についてもご紹介します。
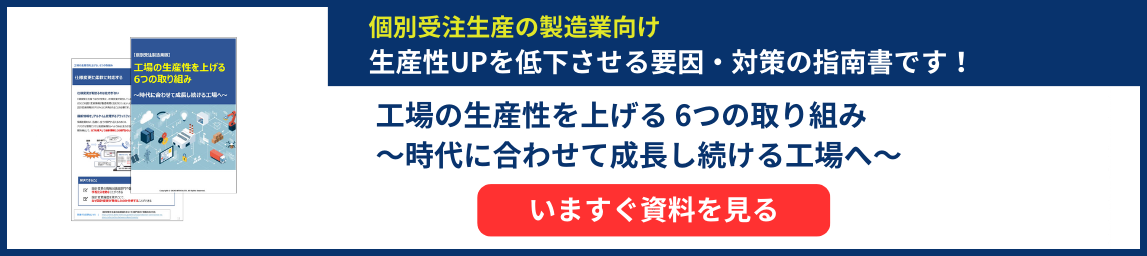
目次
品質不良を正しく知る
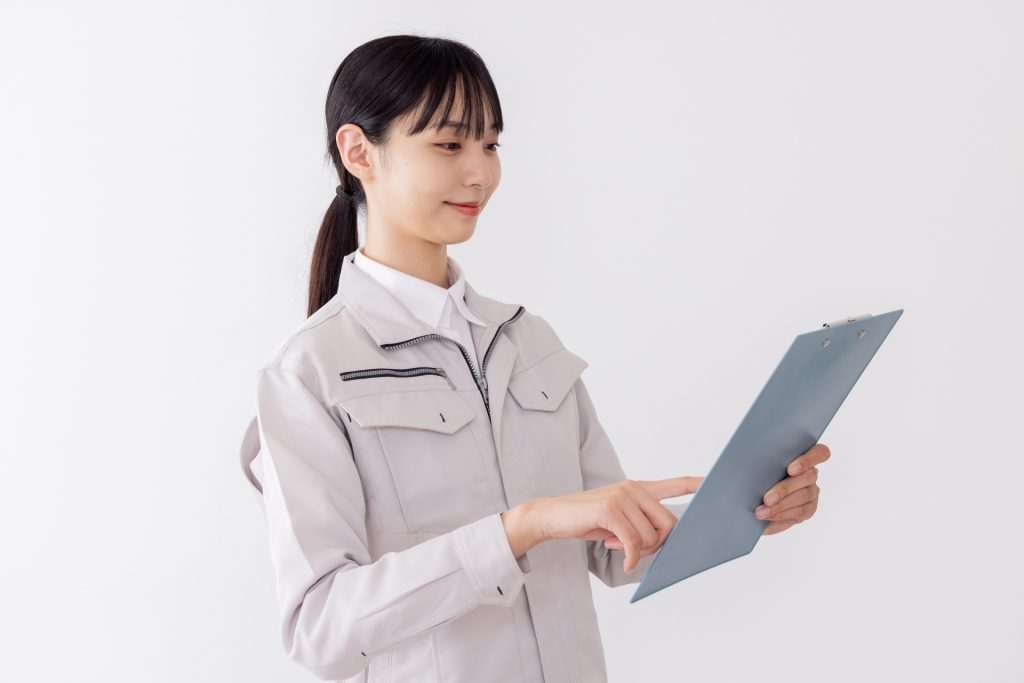
製造業にとって、品質不良の削減は最優先の課題です。
しかし、品質や品質不良といった言葉の本来の意味を理解せずに原因調査を始めると、基準が不明瞭になり中途半端な対策となってしまう危険性があります。
まずは、本章で品質や品質不良の言葉の意味を正しく捉え、基準を明確にしましょう。
品質とは?
品質とは、製品が企業内で設定した項目や顧客ニーズを満たすための基準です。
さらに、製造業において品質は「ねらいの品質(設計品質)」と「できばえの品質(製造品質)」に分かれます。
ねらいの品質(設計品質)とは、顧客の要望を正しく把握した設計と、製造現場で造りやすい製品の設計が実現されたものを指します。
良品の基準を設計図や、仕様書、品質規格などで具体的に示しています。
しばしば顧客の要望のみが重視されるケースがありますが、製造現場が造りづらい設計をしてしまうと却って不良率が高くなってしまう危険性もあるため、バランスの良い設計が必要です。
一方できばえの品質(製造品質)とは、ねらいの品質(設計品質)で作られた設計図や仕様書、品質規格に沿って製造されているかどうかの結果のことです。つまり設計図通りに製造できているかということがカギとなります。
上記の2種類を理解せずにいると、不具合や不良品が発生した際に製造現場だけをターゲットに原因分析を行ってしまうケースが発生してしまいます。
原因の大元が設計段階である可能性もあるため、ねらいの品質(設計品質)とできばえの品質(製造品質)は分けて理解しておきましょう。
品質不良とは?
品質不良とは、良品を決める基準の範囲から外れている製品を指します。
つまり、顧客の要望を満たしていない製品や、設計図や仕様書の基準を満たしていない製品のことです。
品質不良の製品は出荷できないため、コスト増大につながります。
市場に出回ってしまうと、顧客の信頼を失うだけでなく事故の原因になってしまったり、リコールを行わなければならなくなったりと、企業の利益や価値を大きく損なってしまう可能性もあります。
品質不良の原因と4M視点
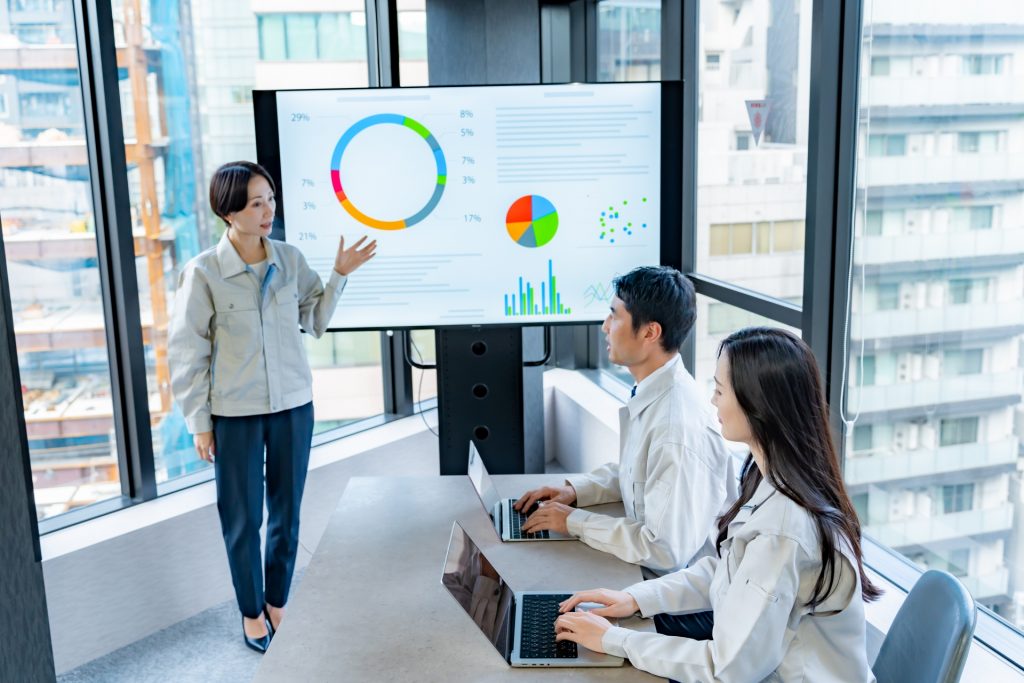
製造業で品質不良が起きてしまった場合、原因は主に4種類に分けて分析できます。
- ヒューマンエラーが原因の品質不良(Man)
- 機械や設備が原因の品質不良(Machine)
- 部品や材料が原因の品質不良(Material)
- 作業方法が原因の品質不良(Method)
上記の4種類は4Mと呼ばれ、製造業ではMan(人)、Machine(機械)、Material(材料)、Method(方法)の要素を管理して、品質向上や問題解決を行っています。
本章では、4Mの視点に分けて品質不良の原因を解説します。
4Mについての詳細は、以下の記事をご参照ください。
ヒューマンエラーが原因の品質不良(Man)
ヒューマンエラーは製造現場で品質不良が起きる原因の一つです。
特に手作業が多い現場や工程では、品質への影響も大きくなってしまいます。
具体的には以下のような例が挙げられます。
- 連日の長時間勤務の疲れから注意力が低下して行うべき作業を怠った
- 新人作業員が不慣れから独自の解釈で誤った作業を行った
- 止めるボタンが緑、開始ボタンが赤になっており、作業時に思い込みにより押すボタンを間違えた
単なる不慣れや疲れが原因となるだけではなく、人間の脳は自分の見たいものだけを見ようとしたり思い込みから抜け出せなかったりする特性があるため、ヒューマンエラーが起こるとも言われています。
機械や設備が原因の品質不良(Machine)
機械や設備が原因で品質不良が起こるパターンもあります。
具体的には以下のような例が挙げられます。
- 設備のメンテナンスを怠り、誤作動が起きた
- 機械の入れ替えを行った直後の調整不良で強度不足などの不良が出た
- 新しく入れた機械の操作ミスによる不良が出た
機械・設備を原因とする品質不良は、メンテナンス不足や老朽化、故障だけがすべてではなく、設備を入れ替えた直後にも品質不良が起きやすい点にも注意が必要です。
部品や材料が原因の品質不良(Material)
使用する部品や材料を原因とした品質不良も一例として挙げられます。
具体的には、以下のような例があります。
- 在庫管理を適切に行っておらず、劣化した部品を使用した
- 購買の際に品質よりも価格の安さを優先し、品質の良くない材料を仕入れて利用した
- 部品や材料の受け入れ時に品質チェックを行わず、不良品と気付かずに使った
部品や材料自体に問題があるケースだけではなく、在庫管理ができていないと部品の経年劣化に気付かずに利用してしまうリスクも想定されます。
作業方法が原因の品質不良(Method)
また、作業方法も品質不良が起こる原因の一つです。
具体的には以下のような例が挙げられます。
- 作業マニュアルが更新されておらず、手順が不明確な作業があった
- 多品種少量生産などで、段取り替えが上手く行っていない
- 工程間のバランスが取れておらず、ラインによっては無理が生じた
- 本来ならば複数工程に分けるべき複雑な作業を一人の作業者に集約させていた
作業方法が原因となるケースでは、作業マニュアルの不備だけでなく、製品に合った生産方式を選択できていない、生産方式や作業方法の改善検討がなされていないといったことが原因となり不良が発生するパターンもあります。
以上のように4Mの変更は、特に不良など品質の悪化が起こりやすくなる変化点です。
4Mの変更があった際には不良が起こらないように、モニタリングや点検回数を増やすなどの対策を行いましょう。
不良率の計算方法や目標数値の目安
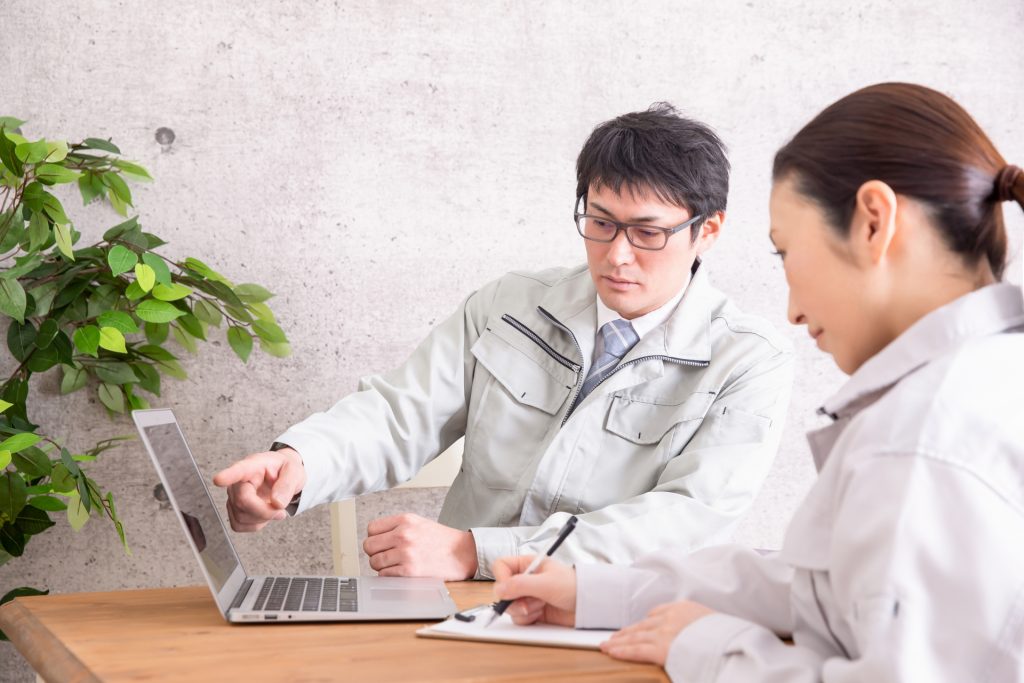
品質不良を削減するための基準として、不良率が挙げられます。
本章では、不良率の計算方法や、間違いやすい歩留まりとの違い、目標とするべき目安の数値についてご紹介します。
不良率の計算方法
不良率は、製造された製品の総数に対しての不良品の割合のことです。
式は以下のように表されます。
不良率(%) = 不良品数 ÷ 生産総数 × 100
例を挙げると、一定期間に製造された製品が10,000個の場合、不良品が200個出てしまったすると、不良率は2%です。
不良率と歩留まり率の違い
不良率と混同しやすい指標に、歩留まり率があります。
歩留まり率とは、原料や素材の投入量に対して、実際に生産できた良品数の割合のことです。
大きな違いは、分母となる数値が不良率では「生産できた総量」であるのに対し、歩留まり率では「投入原材料数」であることです。
不良率の指標「PPM」
次に、不良率の指標となるPPMを解説します。
PPMとは、「Parts Per Million」の略で、製品を100万個製造した場合に不良品数がどれくらいになるのかを表しています。主に大量生産を行う企業で用いられる数値です。
計算方法は以下の通りです。
PPM = 不良品数 ÷ 生産総数 × 1,000,000
PPMを活用する目的には以下が挙げられます。
- 安全性が優先される分野で高品質を実現するため
- サプライチェーン全体での品質管理を行うため
- 世界的な標準と指標を元に品質改善を継続的に行うため
自動車業界や航空宇宙業界では、安全性が最優先されるため、10PPM以下の厳しい基準が適用されているケースも見受けられます。
不良率の現実的な目標設定数値
不良品を出さないようにしたいという心意気は大事ですが、不良品ゼロを目標に掲げてしまうと、膨大な人手や時間がかかる生産効率の悪い製造工程となってしまい、現実的な目標数値ではありません。
一定のばらつきによる不良品の発生を考慮しながら、製品や生産規模、販売価格などによって不良率の目標数値を決めることが重要です。
不良率の目安として、「3σ(シグマ)」、「6σ(シグマ)」というものがあります。
3σとは、1,000個製造したうちの不良品数を3個以下に収めることを目標とする指標です。
不良率で表すと0.3%となり、一般的に品質基準として用いられることが多い数値です。
一方6σとは、10,000個製造したうちの不良品数を3.4個以下に収めることを目標とした指標です。
不良率で表すと0.00034%となり、より安全性が求められる航空宇宙や自動車業界、医療、製薬業界で品質基準として用いられます。
自社の目標を設定する際には、業界の標準や過去データを参考にした現実的な数値目標の設定が重要です。
不良発生時の効果的な対応ステップ
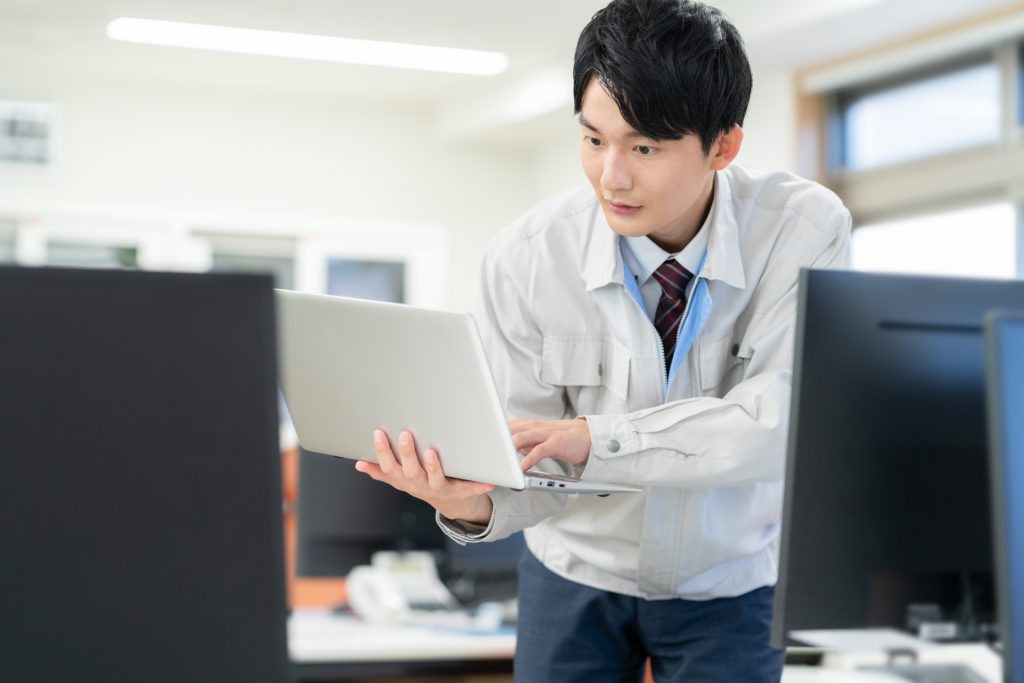
次に、実際に不良が発生してしまった場合に対応すべきステップについて解説します。
具体的には、以下の順番で対応するのが適切です。
- 不良の発生源特定
- 原因究明
- 再発防止の策定と未然防止
- 効果測定
- 標準化
以下で詳しく解説します。
不良の発生源特定
不良が発生した際にまず行うべきことは、発生源の特定です。
明らかに設備の故障でラインが止まってしまったケースなどは発生源が分かりやすいこともありますが、発生源がどこにあるのか特定が難しい場合もあります。
不良が発生した場所や時間、作業者、詳しい状況をヒアリングするなど不良発生時をできるだけ詳細に把握し、発生源の特定を進めていきましょう。
同時に、不良による影響範囲を特定し、社内外に情報共有します。
原因究明
次に、不良の原因を究明します。
前述した4M視点での分析も重要ですが、真の原因の追求のためには下記の方法も有効です。
- なぜなぜ分析
- 特性要因図
なぜなぜ分析
なぜなぜ分析とは、不良など問題が起きて発生源を特定した後に、なぜ特定の事象が発生したのか、「なぜ」が出なくなるまで繰り返して深掘りする分析方法です。
つまり、「なぜ」が出なくなった事象こそが問題の真因であると分析できるのです。
なぜなぜ分析で陥りやすい間違いは、「新人なので経験不足で操作方法を誤った」などと個人の責任や個人の能力を原因としてしまうことです。
なぜなぜ分析では客観的な事象をターゲットとするため、上記の例だと「新人が間違いそうになってしまう機械操作方法」自体をターゲットとする必要があります。
特性要因図
特性要因図は、問題が生じた際の要因をあぶり出すために作成されるもので、完成した図が魚の骨のように見えるため「フィッシュボーン図」とも呼ばれます。
課題を魚の頭部分に書き、枝分かれするように思いつく大きな要因を書き出し、さらに大きな要因を引き起こす要因を書き出していきます。
なぜなぜ分析は事象に対して客観的で明らかな要因を挙げていくのに対し、特性要因図は問題について「思いつく要因」を漏れなく挙げていくため、推測や仮説も含まれる点で大きく異なります。
なぜなぜ分析は課題や原因箇所がはっきりしているケースで利用し、特性要因図は原因箇所が複数で様々な要因が絡み合っていると推測される問題に対して利用するのがおすすめです。
特性要因図に関しては、以下の記事でも詳しく説明していますので、ぜひご確認ください。
【生産管理のDX事例】工場での生産管理の仕事内容とは?生産方式別の特徴をわかりやすく解説
再発防止の策定と未然防止
不良の原因が特定できたら、再発防止策を講じます。再発防止策では以下のポイントに気をつけましょう。
- 実現可能な対策となっているか
- チェックを増やすなど結果的に手間が増える対策になっていないか
- 形骸化する対策ではないか
また、ヒューマンエラーはゼロにはできないため、手作業によるミスを減らしたい場合にはシステム変更やIoT機器の導入なども根本的解決のためには有効です。
不良への対策としては、未然防止の考え方も重要です。
未然防止とは、将来起こりうるリスクに対して、事故やトラブルなどの事象を未然に防ぐことです。
特性要因図などを用いて原因分析を行う中で、今回は問題とならなかったものの将来的に問題となりそうだと推測された事象に関しては、問題が起きる前に対策を講じる必要があります。
効果測定
次に、対策が効果的に働いているかを不良率の推移で確認します。
不良率が目標値以下になっているかどうか、ロットごとに、複数回に分けて検証を行いましょう。
不良率が落ちなければ、原因や対策に問題があるため、再度分析を繰り返します。
標準化
再発防止策の効果が出て不良率が下がったら、対策の標準化を行います。
具体的には、作業マニュアルの改訂や関係各所への通知の徹底などが挙げられます。
不良削減対策のポイント
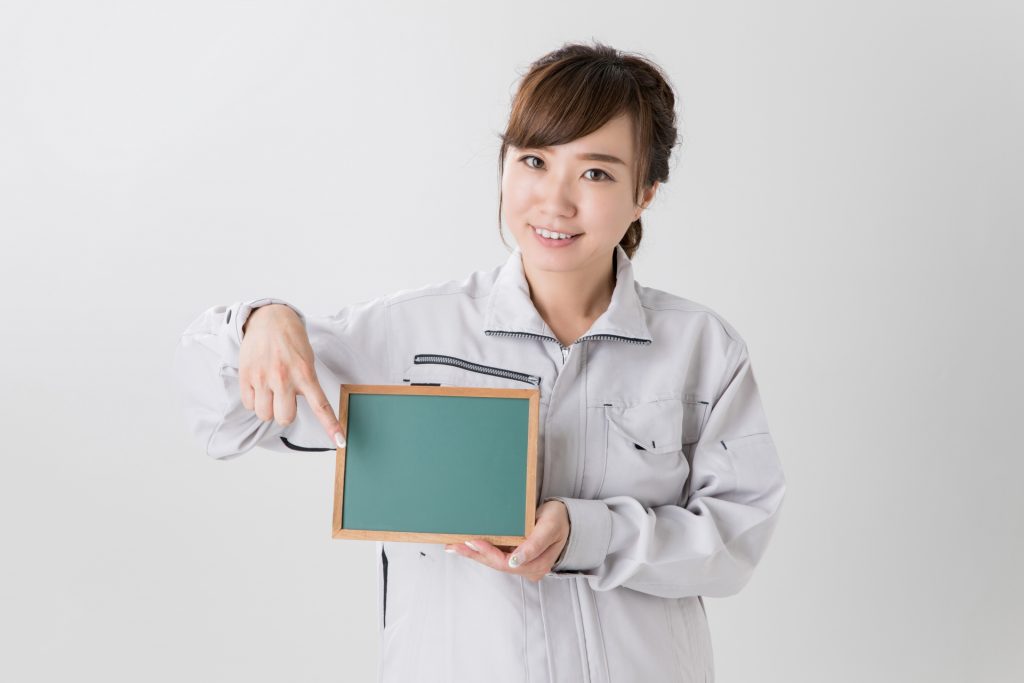
不良削減のための対策のポイントについて解説します。
前章では再発防止策について解説しましたが、本章では不良を起こさないための未然防止の考えのもとで対策をご紹介します。
- 作業標準書の作成や改訂
- 適切なメンテナンス
- 設計時のDRや品質管理の徹底
- 適切なシステム導入
作業標準書の作成や改訂
不良削減のためには、作業標準書の作成や改訂も対策の一つです。
機械自体に付属する操作マニュアルだけに頼らずに、自社独自の作業標準書を作成しましょう。
また、作業標準書はあるものの、改訂を行っておらず形骸化しているパターンもあります。
作業の変更があれば、都度作業標準書の見直しを行い、アップデートしていく必要があります。
適切なメンテナンス
適切なメンテナンスを行うことも不良対策のために重要です。
メンテナンスは形骸化しやすく、場合によっては機械や設備を人の目で見て紙の点検シートにチェックマークをつけるだけといったケースもあります。
未然防止のためにも定期的にメンテナンスを行うだけでなく、IoT機器で数値的な問題がないかをチェックするなど、デジタルを活用した適切なメンテナンスを行うのも一つの手段です。
設計時のDRや品質管理の徹底
製品開発の時点で設計上の問題がないか、DR(デザインレビュー)を行い製造より前に品質管理を行うことも不良対策の一つです。
開発部門だけでなく、生産管理や品質管理、製造部門も交えてDRを開くことも重要です。
設計上問題はなかったとしても、製造工程が複雑でミスやヒューマンエラーを引き起こしやすい状態になってしまう可能性もあるためです。
適切なシステム導入
不良対策としては、適切なシステム導入も有効な手段です。
前述したように、人間の脳は思い込みや自分の見たいものだけが見えてしまう特性があります。
ヒューマンエラーは対策により削減はできるものの、ゼロにはできません。
人間が目で見て判断する部分をシステムに置き換えるだけでも、ヒューマンエラーを削減可能です。
異常検知システムなどIoT化を進めることで、人間の目で見るよりも迅速かつ確実に不良品を出さないための対策が可能です。
また、システム導入の際にはできる限り部署単位ではなく、社内全体で取り組むことも重要です。
部署ごとに異なるシステムを使っていると、情報が部署単位で止まってしまいます。
より広く、社内全体で共有できるシステムを活用できれば、情報共有のための会議を削減したり、品質管理面でも異常に気付きやすいメリットがあります。
品質不良の原因を分析し、現実的な不良率を目標として再発防止を測る
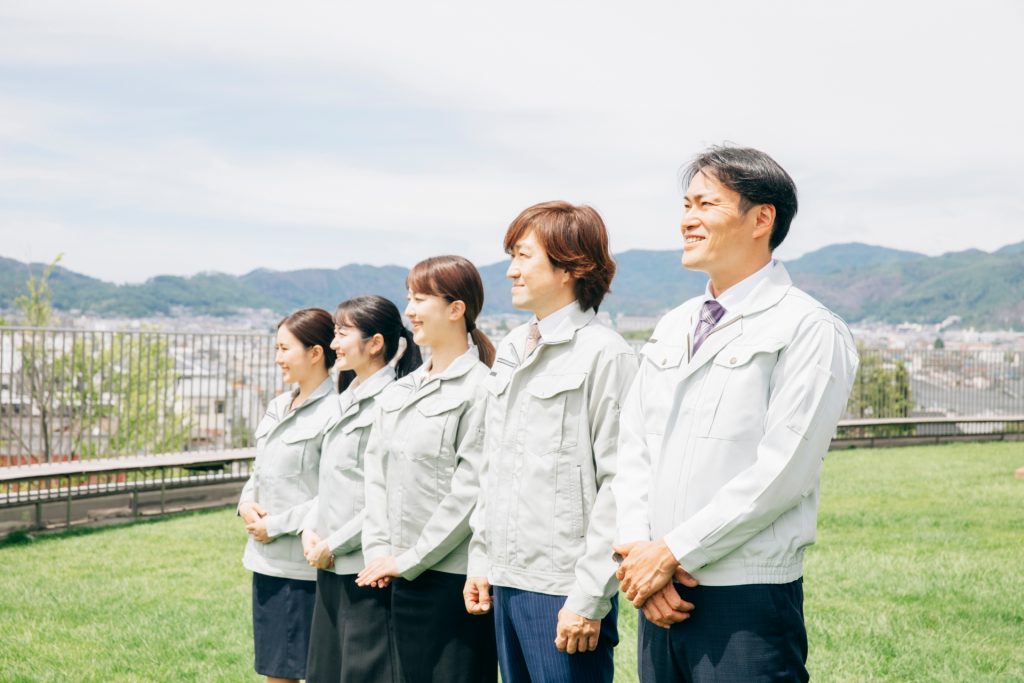
製造業において品質不良は社内での手戻り増加だけでなく、顧客満足度の低下、さらには市場に出回ってしまうと重大な事故につながってしまうなど、企業全体の利益や価値を著しく損なってしまう危険性があります。
ただし、不良率の目標をゼロとするのではなく、現実的な目標を業種や製品によって定めることが重要です。
不良が起きてしまった際には、原因の分析や再発防止、また未然防止の観点から対策を講じていきましょう。
以下のホワイトペーパーでは、品質を維持しながら生産性を上げるための取り組みについてご紹介しておりますので、ぜひご覧ください。
おすすめのお役立ち資料はこちら↓

個別受注生産の製造業向け 生産性UPを低下させる要因・対策の指南書です!
工場の生産性を上げる 6つの取り組み
~時代に合わせて成長し続ける工場へ~
