製造業界において、デジタルトランスフォーメーション(DX)は競争力を高めるために不可欠な取り組みです。
しかし、多くの企業がその具体的な進め方に悩んでいます。
本記事では、工場DXの基礎から実践的なアプローチまで、製造現場の課題解決に直結する情報をお届けします。
目次
工場DXとは
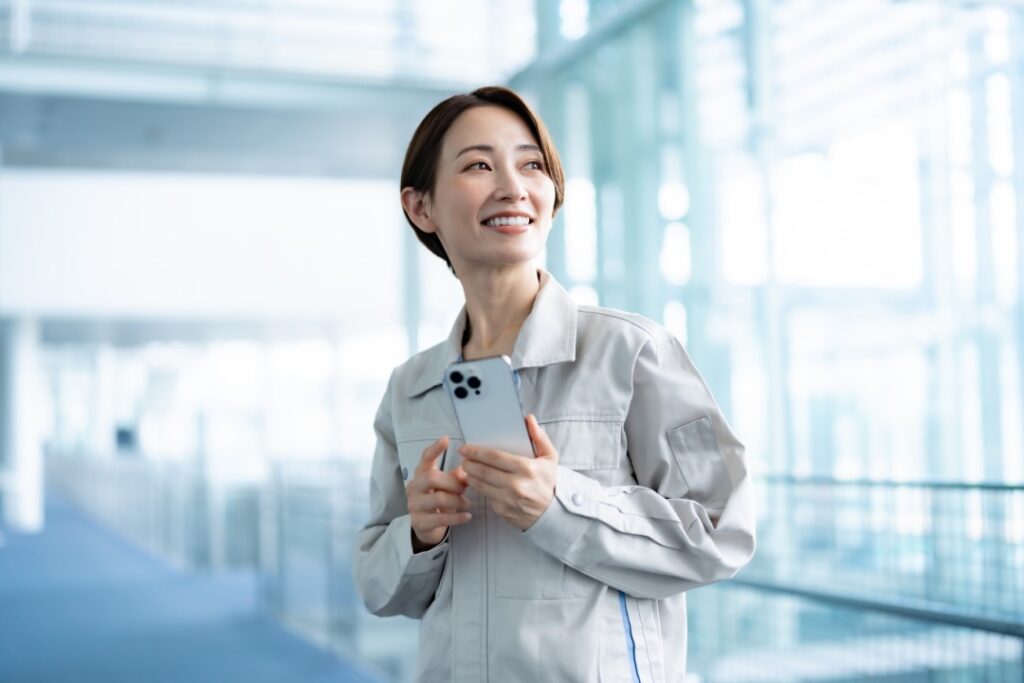
工場DXとは、製造現場においてデジタル技術を活用し、生産システム全体を革新的に変革する取り組みです。
例えば、IoTセンサーやAI技術を活用したデータ収集と分析により、生産プロセスを最適化する手法を指します。
工場DXの目的は、単なる業務の効率化だけではありません。
データに基づいた意思決定を可能にし、生産性向上や品質改善、コスト削減などの成果を生み出すことを目指しています。
さらに、工場DXに取り組むことにより熟練工の技能伝承や予知保全による設備の長寿命化なども期待できるとして、注目を集めています。
なぜ今、工場DXが必要なのか
現在、製造業において工場DXが急務となっている理由は、競争環境の激変と市場ニーズの多様化です。
グローバル化が進行し、海外の企業が最新技術を活用して高品質かつ低価格な製品を大量に生産できるようになり、日本の製造業はかつての優位性を失いつつあります。
消費者のニーズも「モノ消費」から「コト消費」へと移行し、製品に求められる価値が変化している背景も影響しています。
加えて、日本国内では少子高齢化による労働力不足の深刻化も課題です。
従来の生産体制では人手不足を補うことが難しくなっており、効率的な生産体制の確立が急務な状態です。
これらの問題に対応するため、工場DXは不可欠な戦略となっています。
デジタル技術を活用することで、業務の自動化やデータに基づいた迅速な意思決定が可能となり、競争力の維持・向上が期待されています。
従来の改善活動とDXの違い
従来の改善活動とDXは、どちらも業務を改善する手段ですが、その目的やアプローチには大きな違いがあります。
従来の改善活動は、主に現場の効率化やコスト削減を目指し、既存のプロセスを少しずつ改善していく「カイゼン」手法が中心でした。
これは短期的な成果を得やすい一方、抜本的な構造改革には向いていません。
一方、DXは単なる効率化にとどまらず、デジタル技術を活用して業務プロセス全体やビジネスモデルそのものを再設計し、競争力の源泉を構築することを目的としています。
DXでは、IoTやAIといった技術を取り入れ、データに基づく意思決定や自動化を推進し、業務の抜本的な変革を実現します。
従来の改善活動が「現状の延長線上」にあるのに対し、DXは未来を見据えた「革新的な変革」と言えます。
日本のDX市場動向
日本のDX市場は、2022年度時点で2兆7,277億円と推定され、2030年度には6兆5,195億円にまで拡大すると予測されています。
製造業においてもDX市場は急速に拡大しています。
富士キメラ総研の調査によると、2022年度の市場規模は2,990億円であり、2030年には8,130億円に達する見込みです。
企業の約67.8%がDXへの取り組みを開始または検討段階にあり、デジタル技術の活用に対する意識が高まっています。
特に製造業では、デジタル技術を活用する企業が60%を超え、生産性向上や競争力強化に向けた戦略的投資が加速しています。
工場DXの最新のトレンド
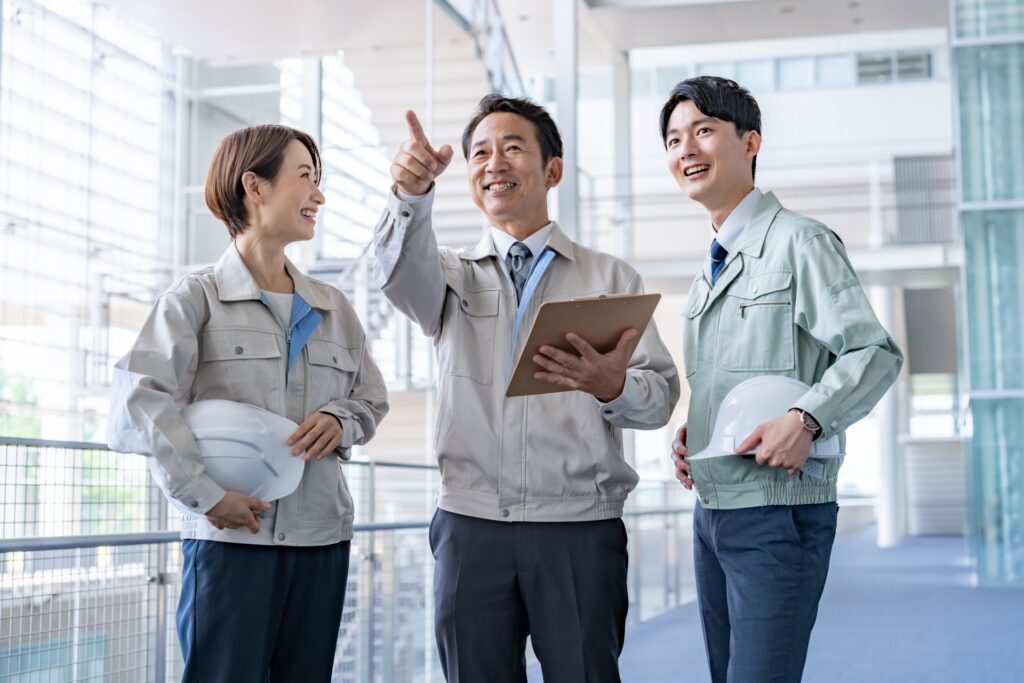
製造業界におけるDXは、2024年に入り新たな展開を見せています。
デジタル技術の進化と製造現場のニーズが融合し、より実践的なソリューションが登場しています。
特に注目すべき工場DXとして、以下のようなDXへの取り組みがあります。
- 予測保全システム
- デジタルツイン
- スマートファクトリー
- スマート製造の推進
- GX(グリーントランスフォーメーション)との連携
これらの工場DXへの取り組みは、製造業の競争力強化に直結する重要な要素です。
以下では、各トレンドの具体的な内容と実践方法について、順を追って解説していきます。
予測保全システム
予測保全システムは、製造現場における設備保全の概念を根本から変革する革新的なソリューションです。
予測保全システムは、IoTセンサーとAI技術を組み合わせ、設備の状態をリアルタイムで監視・分析します。
従来の定期保守や事後保全と異なり、設備の異常を事前に検知し、最適なタイミングでメンテナンスを実施することが可能です。
具体的な効果として、以下の3点が挙げられます。
- 保守コストの大幅な削減(従来比40%減)
- 設備の稼働率向上(ダウンタイム70%減)
- 生産性の改善(設備効率25-30%向上)
特に個別受注生産を行う製造現場では、設備の突発的な故障が製造リードタイムに大きな影響を与えます。
予測保全システムの導入により、計画的な保守が可能となり、安定した生産体制の構築が期待できます。
デジタルツイン
デジタルツインは、物理的な製造設備やプロセスをリアルタイムでデジタル上に再現する技術で、工場DXの中でも注目を集めています。
デジタルツインにより、製造現場のデータをリアルタイムで収集・解析し、仮想空間でシミュレーションを行うことが可能です。
生産効率の向上や設備の最適化、メンテナンスのタイミングの最適化といった効果が得られます。
また、デジタルツインは、予測保全やプロセス改善にも大きな役割を果たします。
例えば、設備の故障予測や生産ラインの最適化をシミュレーションすることで、実際の稼働に移る前に問題を特定し、コスト削減やダウンタイムの短縮が可能です。
デジタルツインの市場は、デジタルツインの利用が今後さらに拡大し、2027年には735億ドルに達する見込みです。
製造現場における競争力強化のために、デジタルツインの導入が期待されています。
スマートファクトリー
スマートファクトリーは、工場DXの最先端を行く概念であり、IoT、AI、ビッグデータなどの先端技術を駆使して、生産プロセス全体をデジタル化・自動化した次世代の工場です。
スマートファクトリーの導入は、製造業における競争力を高めるために不可欠です。Precedenceの調査によると、グローバルなスマートファクトリー市場は2034年までに約3,863億ドルに成長する見通しです。
企業はこの技術を導入することで、効率的な生産体制を確立し、さらには環境負荷の軽減や持続可能な成長を実現することが期待されています。
スマート製造の推進
スマート製造は、IoTセンサーやAI技術を活用して製造プロセス全体をデジタル化し、生産性と品質を同時に向上させる先進的な製造手法です。
具体的には、以下のような手法が挙げられます。
- リアルタイムモニタリング:生産ラインの稼働状況をリアルタイムで把握し、迅速な意思決定を実現
- 予測分析:AIを用いて生産量や品質を予測し、最適な生産計画を立案
- 自動最適化:生産パラメータをAIが自動調整し、常に最適な状態を維持
- サプライチェーン連携:取引先とのデータ連携により、需要予測の精度向上や在庫最適化を実現
これらの取り組みにより、工場はスマート製造を推進し、競争力の向上やコストパフォーマンスの改善を実現できます。
GX(グリーントランスフォーメーション)との連携
GXは、環境に配慮した持続可能な社会を目指すための企業変革を指し、製造業においても重要な取り組みです。
工場DXとの連携により、GXの推進はさらに加速します。
例えば、DXで導入されるIoTやAI技術を活用することで、エネルギー消費の最適化や排出ガスの削減が可能になり、環境負荷を低減できます。
また、GXは単なる環境対策に留まらず、コスト削減や新たなビジネス機会の創出にもつながる取り組みです。
エネルギー効率の改善や廃棄物削減は、長期的な運用コストの削減を実現するだけでなく、環境に配慮した製品を求める消費者からの支持を得るという点で競争優位性をもたらします。GXとDXを連携させることは、企業の持続可能な成長に向けた取り組みとして期待されています。
工場DXでおすすめのツール
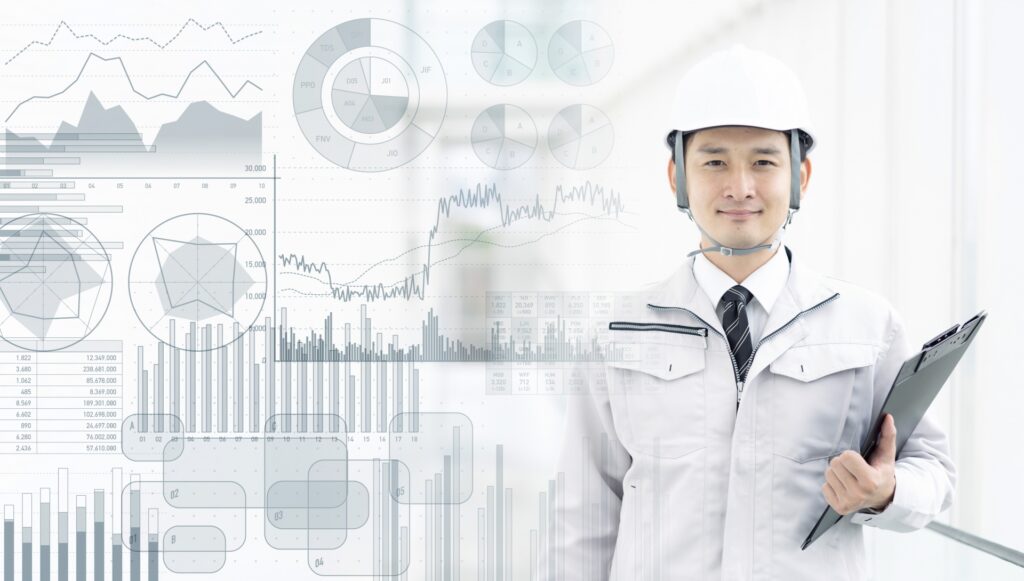
製造業のデジタル変革を推進するためのツール選びは、企業の競争力を左右する重要な戦略です。
最新のデジタル技術を活用し、生産性と効率性を飛躍的に向上させるツールが次々と登場しています。
工場DXを成功に導くためのおすすめツールは、以下のツールがあります。
- プロジェクト管理ツール
- IoT(Internet of Things)デバイス
- BOM(部品表)システム
- RFID(自動認識)システム
- AI(人工知能)および機械学習ツール
- ERP(企業資源計画)システム
- PLM(製品ライフサイクル管理)ソフトウェア
- CAD/CAM(コンピュータ支援設計/製造)ソフトウェア
各ツールの詳細と具体的な活用方法について、以降で詳しく解説していきます。
プロジェクト管理ツール
プロジェクト管理ツールは、製造現場における生産計画から進捗管理まで、複雑な工程を一元管理するデジタルソリューションです。
プロジェクト管理ツールは、プロジェクトの進捗管理やタスクの割り当て、スケジュールの調整を一元管理し、リアルタイムでの確認や更新が可能です。
製造業の複雑なプロジェクトでも、チーム間のコミュニケーションを円滑にし、各タスクの進行状況を可視化することで、効率的なプロジェクト運営を実現します。
IoT(Internet of Things)デバイス
IoTデバイスは、製造現場のあらゆるデータをリアルタイムで収集・分析し、生産プロセスの最適化を実現するツールです。
個別受注生産の製造現場では、製品ごとに異なる製造条件や品質要件への対応が求められますが、IoTデバイスの活用によりこれらの課題を効果的に解決できます。
また、製造現場での具体的な活用方法として、設備の状態監視があげられます。
温度、圧力、振動などのデータをリアルタイムで収集し、異常の予兆を早期に検知できます。
さらに、製造工程の進捗管理では、各工程の稼働状況を自動的に記録し、納期管理の精度を向上させます。
BOM(部品表)システム
BOM(部品表)システムは、個別受注生産を行う製造業において、生産管理の根幹を支える戦略的なデジタルツールです。
製品を構成するすべての部品と材料の情報を一元管理し、受注後の仕様変更にも柔軟に対応できる機能です。
特に、部品表の統合管理と設計・生産管理の連携を実現することで、原価管理の精緻化と製造リードタイムの短縮に大きく貢献します。
複雑な製品構造を可視化し、設計から生産までの一貫したデータ管理を可能にする、まさに製造業DXの要となるシステムと言えます。
RFID(自動認識)システム
RFIDシステムは、製品や部品に取り付けたICタグを使って、無線で情報の読み取りや書き込みを行う技術です。
工場DXにおいては、RFIDを活用することで、製造現場での物品管理や在庫管理が効率化され、作業の正確性やスピードが向上します。
タグに記録された情報はデバイスを使って非接触で読み取れるため、従来のバーコードスキャンよりも作業負担を軽減し、エラーの発生も防げます。
RFIDシステムを導入することで、リアルタイムで製品や部品の位置や状態を把握できるため、在庫管理や物流プロセスの最適化が可能です。
また、製造ラインの自動化にも対応し、リードタイムの短縮やトレーサビリティの向上が期待されます。
特に、複雑なサプライチェーンを持つ企業にとって、RFIDは生産管理の強力なツールです。
AI(人工知能)および機械学習ツール
AI(人工知能)や機械学習ツールは、製造業におけるDX推進において欠かせない技術です。
製造業の工場DXにおいて、AI(人工知能)および機械学習ツールは次のようなメリットを提供します。
生産予測
AIは過去の生産データや市場動向を分析し、未来の生産量を見積もることで、需要予測を精緻化し、在庫過多や不足を防ぎます。
品質管理
リアルタイムでセンサーデータを分析し、製品の品質に関わる指標を監視します。これにより、製造プロセスを最適化し、不良品を減らします。
故障予知
機械学習を用いた故障予測モデルによって、設備の故障リスクを予測し、計画的なメンテナンスを可能にします。
これらのAIおよび機械学習ツールの導入により、生産性の向上、品質の改善、コスト削減、そして意思決定の迅速化が期待できます。
特に大量のデータを扱う製造業において、その効果は顕著に現れます。
ERP(企業資源計画)システム
ERP(企業資源計画)システムは、生産管理、在庫管理、購買、財務管理など、企業のさまざまな業務プロセスを統合し、一元管理するツールです。
個別受注生産の製造現場では、設計から製造、原価管理まで、各部門間での情報連携が課題となっていますが、ERPシステムの導入によりこれらの課題を効率的に解決できます。
例えば、受注情報から必要な部材の手配、製造スケジュールまでを一元管理し、製造リードタイムを短縮します。
また、原価管理面では、設計変更に伴う部品構成の変更や工数の変動をリアルタイムで把握し、収益性の管理精度を向上させることが可能です。
PLM(製品ライフサイクル管理)ソフトウェア
PLMソフトウェアは、製品の企画から設計、製造、保守に至るまでの全ライフサイクルを一元管理するソリューションです。
個別受注生産の製造現場では、製品ごとに異なる仕様や設計変更への対応が課題となっていますが、PLMソフトウェアの導入によりこれらの課題を効率的に解決できます。
主な活用シーンとして、まず設計情報の統合管理があります。図面データや部品表を一元管理し、設計変更の影響を製造工程まで追跡することが可能です。
また、開発プロセスの効率化では、過去の設計資産を活用し、類似製品の開発期間を短縮することが可能です。
さらに、製品品質の向上では、設計段階から製造性を考慮した検討が可能となり、手戻りを防止します。
CAD/CAM(コンピュータ支援設計/製造)ソフトウェア
CAD/CAM(コンピュータ支援設計/製造)ソフトウェアは、製造業における設計から製造までのプロセスを効率化するためのツールです。
CADは、2Dや3Dの精密な設計図を作成するために使用され、設計者が詳細な製品モデルを構築し、リアルタイムで設計変更を行うことが可能です。
これにより、設計ミスの削減や設計プロセスの短縮が実現します。
一方、CAMは、CADで作成された設計データを基に、製造工程を自動化して効率化するソフトウェアです。
これにより、NC(数値制御)機械などの製造機器が正確に動作し、製品の品質向上と生産速度の向上が期待されます。
すぐに始められる工場DX取り組みの事例
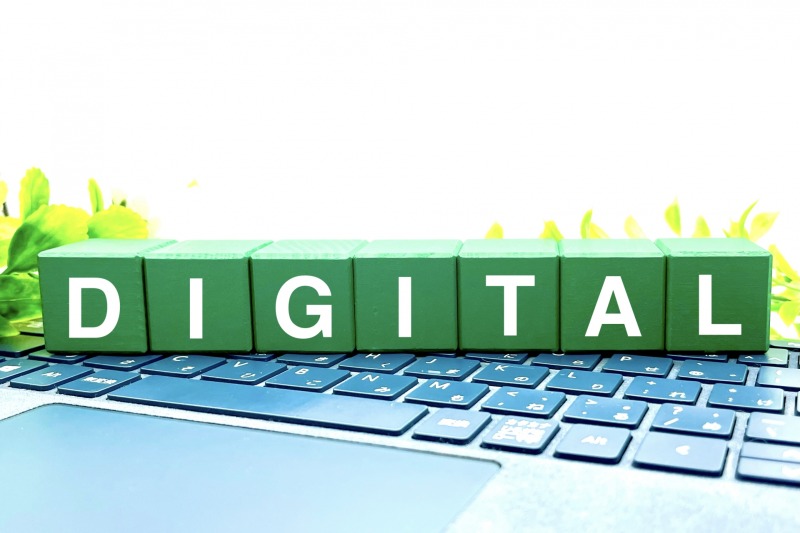
造現場のDXは、大規模なシステム投資から始める必要はありません。
既存の設備や業務プロセスに、デジタル技術を段階的に導入することで、着実な成果を上げることができます。
特に個別受注生産の製造現場では、以下のような施策から始めることで、効果的なDX推進が可能です。
- メーター監視の自動化
- 紙帳票のデジタル化
- 遠隔サポートの実現
- コミュニケーションのデジタル化
- 生産データの可視化
これらの施策は、比較的小規模な投資で開始でき、短期間で効果を実感できる取り組みです。
各施策の具体的な内容と実践方法について、順を追って解説していきます。
メーター監視の自動化
メーター監視の自動化は、工場DXの第一歩として取り組みやすく、即効性のある施策です。
従来、作業員が定期的に行っていたアナログメーターの目視確認をIoTカメラとクラウドサービスを組み合わせて自動化することで、大きな効果が得られます。
この施策の導入により、作業員の巡回点検にかかる工数を大幅に削減し、より付加価値の高い業務に時間を振り向けることが可能です。
また、24時間365日の常時監視により、異常の早期発見と迅速な対応が実現します。
紙帳票のデジタル化
従来、製造現場では手書きの書類や帳票が多く使用されており、情報の収集や管理に多くの時間と手間がかかっていました。
しかし、AIを活用したOCR(光学文字認識)技術を導入することで、これらの紙帳票を自動的に高精度でデジタル化できます。
このデジタル化によって、手作業での入力ミスが減少し、データの検索・共有が簡単に処理可能になります。
また、クラウドシステムを利用すれば、工場内外の複数の部署でリアルタイムに情報を共有できるため、業務の効率化が図れます。
紙ベースの管理から解放され、工場の運営がスムーズに進むようになることが期待できます。
遠隔サポートの実現
遠隔サポートの実現は、工場DXの重要な施策の一つであり、特に人手不足や技術継承の課題がある製造業において効果的です。
特に、ウェアラブルデバイスやAR(拡張現実)技術を活用することで、現場作業員は専門家からのサポートをリアルタイムで受けることが可能です。
例えば、RealWearのようなウェアラブルデバイスを使用することで、音声コマンドでマニュアルを参照したり、問題を映像で共有したりすることができ、ハンズフリーで作業を行うことができます。
このような遠隔サポートにより、作業員は迅速に問題を解決できるため、作業効率が向上し、ダウンタイムの削減につながります。
コミュニケーションのデジタル化
従来、対面でのやり取りや紙ベースでの情報伝達が中心でしたが、デジタルツールの導入により、リアルタイムでの情報共有が可能です。
例えば、チャットツールやプロジェクト管理ソフトウェアを導入することで、現場の作業員と管理者、さらには異なる部門間でのコミュニケーションが円滑になります。
問題の早期発見や迅速な対応が可能となり、製造プロセスの効率化が期待できます。
また、ビデオ会議システムを活用すれば、遠隔地にいる専門家からのサポートを受けながら、現場の状況を共有し、適切なアドバイスを受けることもできます。
このようにデジタル化されたコミュニケーションは、製造現場の生産性を高めるための基盤として期待できます。
生産データの可視化
生産データの可視化は、データを単に集めるだけでなく、視覚的に表現することで、製品の生産状況や業務の効率をリアルタイムで把握できます。
このアプローチにより、経営層から現場の作業者まで、誰もがデータに基づいた迅速な意思決定を行うことが可能です。
これにより、現場の課題を明確にし、改善策を迅速に検討することができるため、生産性の向上やコスト削減に直結します。
例えば、BIツールやダッシュボードを用いて、重要なKPI(重要業績評価指標)をリアルタイムで表示することが効果的です。
生産データの可視化は、製造業の競争力を高めるための基盤となる取り組みです。
工場特有のDX課題と解決策
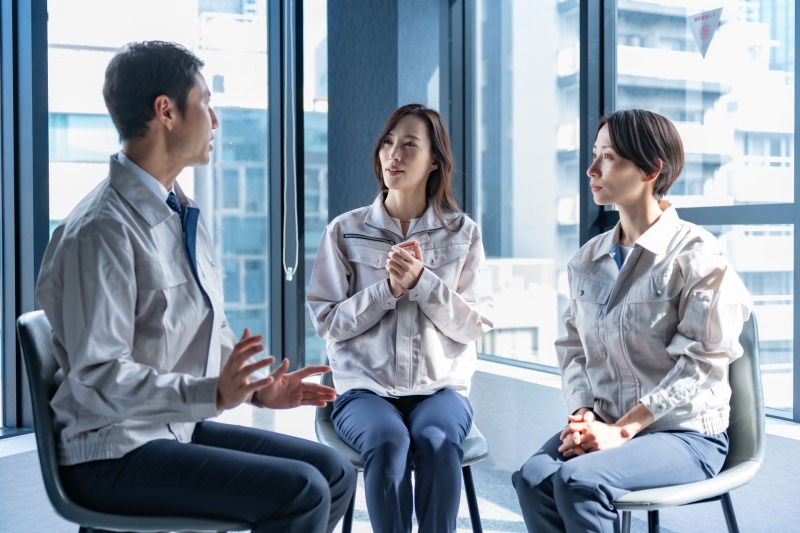
製造業のDX推進には特有の課題が存在します。
これらの課題を理解し、適切な解決策を講じることでスムーズなDXが可能です。
- レガシーシステムとの統合問題
- 現場作業者のデジタルスキル向上
- ツール選定の難易度が高い
以下では、それぞれの工場DX課題や解決策について詳しく解説します。
レガシーシステムとの統合問題
レガシーシステムとの統合問題は、多くの製造業で直面するDXの課題の一つです。
古いシステムや設備が新しいデジタル技術と連携できないことが、情報の断絶や業務プロセスの非効率を引き起こします。
これを解決するためには、まず既存のレガシーシステムの評価を行い、どの部分が新しい技術と統合可能かを明確にすることが必要です。
次に、データ収集のためのインターフェースやセンサーを追加することで、リアルタイムでのデータ可視化を実現します。
例えば、アナログメーターにIoTカメラを設置してデータをデジタル化する方法やAPIを利用して新旧システム間でのデータ連携を図るアプローチがあります。
さらに、段階的にシステムを更新していく「スモールスタート」の戦略を採用することで、リスクを抑えつつ効果的にDXを進めることが可能です。
現場作業者のデジタルスキル向上
多くの製造現場では、既存の業務プロセスをデジタル化する際、作業者が新しい技術やツールを使いこなせないことが問題になります。
そのため、現場作業者のスキル向上が不可欠です。
例えば、定期的な研修やトレーニングプログラムの実施によりデジタルツールやソフトウェアの使い方を学ぶことで、
作業者は新しい技術に対する抵抗感を減らし、業務効率を高めることができます。
また、オンラインプラットフォームを活用したeラーニングも、柔軟にスキルを習得する手段として有効です。
このような取り組みを通じて、製造現場全体のデジタルスキルを向上させ、DX推進の基盤を固めることができます。
ツール選定の難易度が高い
製造業のDXを推進する上で、適切なITツールの選定は極めて重要ですが、そのプロセスは多くの企業にとって難易度が高いものとなっています。
特に、自社の課題や目的に即したツールを見極めるためには、専門的な知識と経験が求められます。
予算を抑えた結果、パッケージツールに業務フローを無理に合わせることで、かえって作業工数が増加するといった結果になりかねません。
また、必要以上の要件でシステム開発を行い、現場の従業員がツールを使いこなせない場合、システムは形骸化し、従来のアナログ管理に逆戻りしてしまう恐れもあります。
これを避けるためには、外部のDX支援を依頼し、業務フローの見直しや適切なツールの導入支援を受けることが効果的です。
工場DXの実践に向けてできることから始めよう
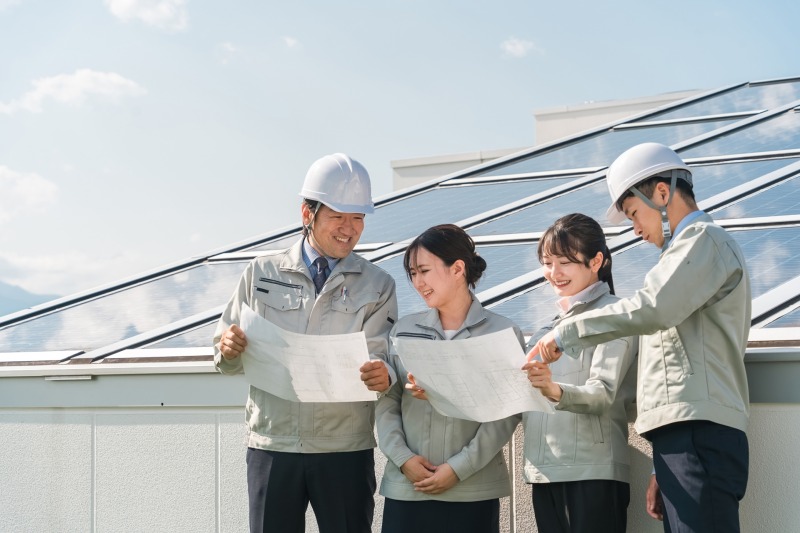
工場DXは、競争力を高めるために不可欠な取り組みです。
しかし、多くの企業が具体的なステップを踏むことに悩んでいます。
まずは、既存の業務プロセスを見直し、小さな改善から始めることが重要です。
日常業務の中で取り入れられる簡単なデジタルツールを活用することや業務フローの可視化、データ収集の自動化など、段階的に進められる施策を考慮しましょう。
このようなスモールスタートのアプローチは、DXの導入に対する抵抗感を減少させ、成功体験を積むことで、さらなる拡大へとつながります。
さらに、製造業のDXを効果的に進めるための具体的な知識や手法を学ぶことができる「製造業のDX推進ガイドブック」をぜひご活用ください。
製造業の効率化を実現するためのDXの重要性や導入方法について詳しく解説しています。
おすすめのお役立ち資料はこちら↓

製造業の効率化を実現する!
製造業のDX推進ガイドブック
