製造業やサービス業において、無駄の多い生産プロセスに悩んでいる方も多いのではないでしょうか。
生産効率の悪化やコスト増大は、納期遅延や品質低下だけでなく、顧客満足度や市場競争力の低下にも直結する重大な課題となります。
本記事では、こうした課題を解決するために注目される「リーン生産方式」について、基礎知識からトヨタ生産方式(TPS)との違い、導入のメリット・デメリットまで徹底的に解説します。
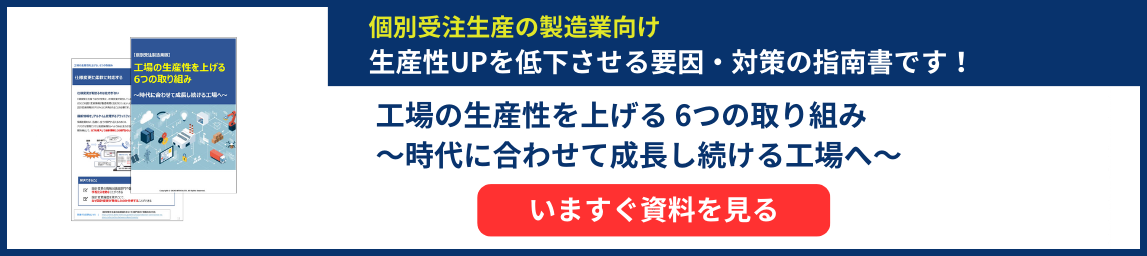
目次
リーン生産方式とは?
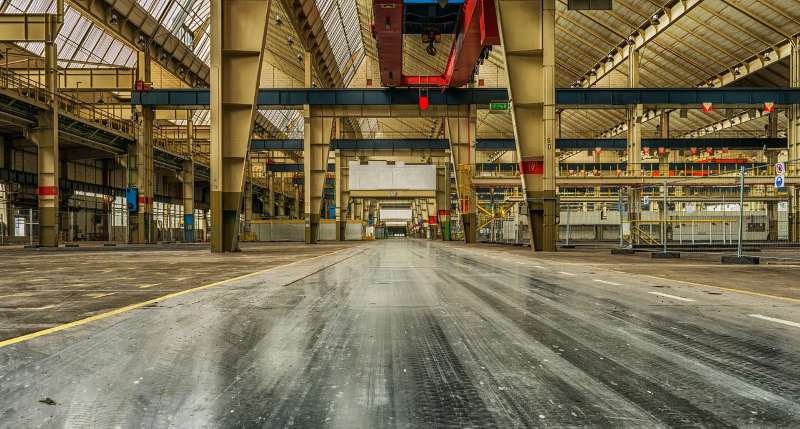
リーン生産方式は、製造現場の無駄を徹底的に排除し、生産効率を最大限に高めるための考え方です。
もともとは日本のトヨタ自動車で確立された生産管理手法(TPS)が基礎になっていますが、その後、海外の研究者によって理論化・体系化され、今では業界や国を超えて広く活用されています。
リーン生産方式とトヨタ生産方式(TPS)の違い
リーン生産方式とトヨタ生産方式(TPS)は密接に関係していますが、その目的や応用範囲には違いがあります。
TPSはトヨタ社内の文化や現場力を前提とした実践型の仕組みで、「ジャスト・イン・タイム」や「自働化」など独自の用語が特徴です。
一方、リーン生産方式はTPSの考えを理論的に再構築し、一般向けに体系化されたものです。
例えば、TPSの思想を「価値の流れ」や「プル型生産」といった共通言語に置き換えることで、製造業以外の業種にも展開しやすくなっています。
つまり、リーンはTPSを誰でも使える形にしたグローバルな改善手法だといえます。
リーン生産方式の基本原則
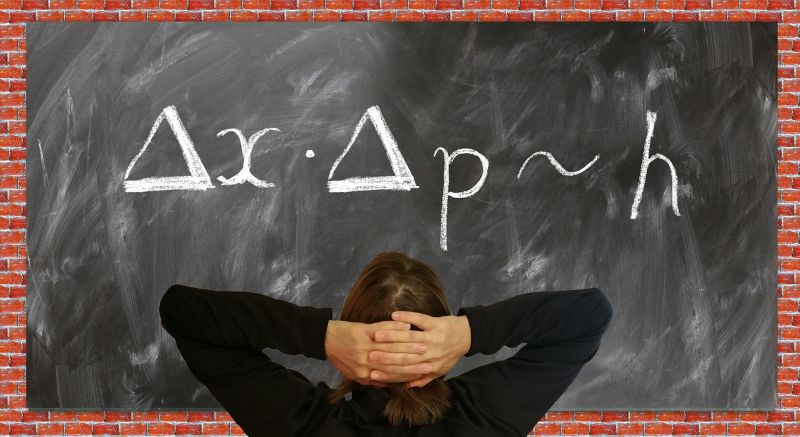
リーン生産方式には、どの業種でも応用できる「5つの基本原則」があります。
これらはすべて無駄をなくして価値を最大化することを目的とした考え方であり、業務の見直しや改善活動に生かせます。
ここでは、それぞれの原則について詳しく見ていきましょう。
顧客視点で価値を定義する
リーン生産方式において重要なのは、「価値」をお客さまの立場で定義することです。
企業側が良いと思っていても、顧客が求めていない作業や機能は無駄に該当します。
例えば、過剰な包装や不要な工程は、品質に貢献しない限り価値ではありません。
そのため、まずは顧客が何に対してお金を払いたいのかを明確にし、それ以外の要素を極力排除する姿勢が求められます。
価値の流れを見える化する
次に大切なのは、製品やサービスが顧客に届くまでの流れを可視化することです。
この流れを「バリューストリーム」と呼びます。
受注から納品までの各工程において、どこに無駄や滞留があるかを洗い出すことで、効率化の余地が明らかになります。
例えば、帳票処理や承認フローが多すぎて時間がかかっている場合、それは改善すべきポイントです。
目に見える形で全体像を把握することで、チーム内の認識をそろえ、改善につなげやすくなります。
フローを最適化する
無駄を特定したあとは、業務の流れ(フロー)をできるだけ止めずにスムーズに進める工夫が必要です。
具体例として、生産ラインで部品の移動や段取り替えに時間がかかっていると、それだけでリードタイムが延びコストも増加します。
これを避けるためには、工程間の無駄な待機時間を減らしたり、作業の並列化を進めたりといった対策が有効です。
流れが止まらなければ生産全体がスピーディかつ安定して進行し、トラブルの早期発見にもつながります。
プル型生産方式を導入する
プル型生産とは、顧客の需要に合わせて必要なものを必要なタイミングで作る方式です。
プル型生産に対して、あらかじめ在庫を作り込む方式は「プッシュ型」と呼ばれます。
プル型では、後工程からの指示をもとに生産を開始するため、在庫の無駄や作りすぎのリスクを抑えることが可能です。
需要主導の仕組みが安定した生産とコスト管理を可能にします。
継続的な改善を行う
リーン生産方式は、改善を繰り返すことによって、より良い状態を目指していく取り組みです。
現場の声を生かし小さな改善を積み重ねることで、少しずつ理想の業務形態に近づけていくことが可能です。
例えば、作業手順の見直しや道具の配置改善など、ささいな工夫でも積み重ねれば大きな成果につながります。
また、チーム全体で改善文化を共有することで、社員のモチベーションやエンゲージメントの向上にも寄与します。
リーン生産方式における「7つの無駄」とは
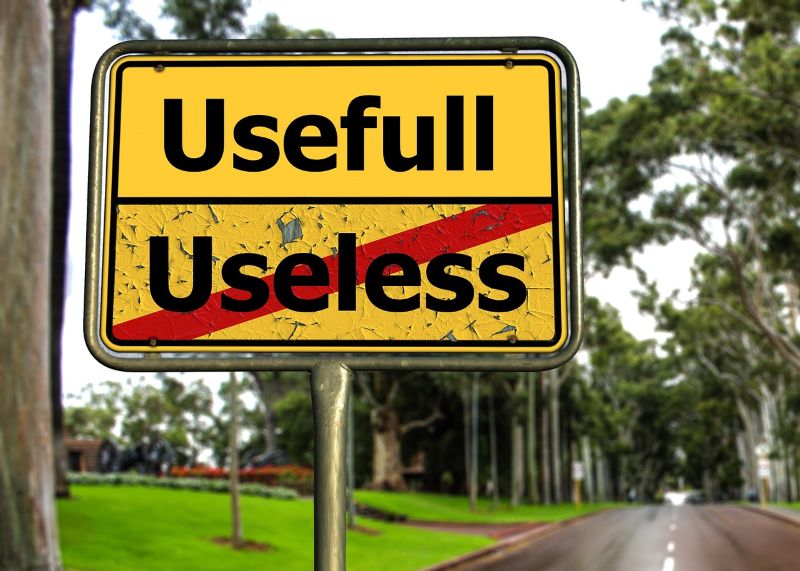
リーン生産方式では、生産や業務の効率を妨げる7つの無駄を明確に定義しています。
これらの無駄を把握し改善していくことで、コスト削減や品質向上、働きやすい職場づくりが実現可能になります。
以下では、それぞれの無駄について具体的に見ていきましょう。
作りすぎの無駄
作りすぎとは、実際の需要を超えて余分に製品をつくってしまうことによって発生する無駄です。
過剰な在庫は保管スペースを圧迫し、保管コストや品質劣化、廃棄のリスクを招きます。
具体的には、季節商品の需要を見誤って大量生産し、売れ残って値引きや廃棄に追い込まれるケースなどが挙げられます。
このような無駄を避けるためには、需要予測の精度向上とともに必要なときに必要な量だけを生産するジャスト・イン・タイムの仕組みが効果的です。
手持ち無沙汰の無駄
手持ち無沙汰の無駄は、作業員が仕事の開始や次の作業を待つ時間が発生している状態です。
例えば、部品が届かず生産がストップしてしまう、上司の承認を待って業務が止まるなど、人材が十分に活用されない状況は大きな非効率につながります。
この無駄を改善するには、業務フローの見直しや工程間の連携強化が重要です。
また、業務の可視化やスケジューリングの精度を高めることで、待機時間を減らし生産性の向上が期待できます。
運搬の無駄
運搬の無駄とは、モノや情報を必要以上に移動させてしまうことによって生じる非効率な動きです。
部品を毎回遠くの倉庫に取りに行く作業や、書類を複数の部署で回覧する手間などが該当します。
こうした動作は直接的な価値を生まず、移動時間や労力が無駄になります。
この無駄を減らすには、作業動線やレイアウトの見直し、必要なものがすぐに手に取れるような配置改善が不可欠です。
加工の無駄
加工の無駄とは、顧客にとって不要な工程や過剰な品質対応によって発生する余計な作業(必要以上の仕上げ作業や、本来不要な検査)です。
これにより時間もコストも無駄に消費され、本来提供すべき価値から逸脱してしまいます。
加工の無駄を防ぐには、顧客の要望を正しく把握しそれに応じた適正な品質・仕様での対応を徹底することが必要です。
在庫の無駄
在庫の無駄は、原材料や仕掛品、完成品を必要以上に保有してしまうことで生じます。
多すぎる在庫はスペースを圧迫し、在庫管理の手間や保管コストの増大、品質劣化のリスクにつながりかねません。
具体的には、部品を過剰に仕入れて棚に山積みにしたまま長期間使われないケースなどが該当します。
このような無駄を減らすには、在庫の適正量を見極め、リアルタイムでの在庫管理や発注精度を向上させることが大切です。
在庫管理について詳しく知りたい方は下記をご覧ください。
安全在庫とは?計算式やメリット、適正在庫や発注点との違い、取り入れる注意点について解説!
動作の無駄
動作の無駄とは、作業者が探す・しゃがむ・伸ばすなど、必要以上の動きを伴うことで生産性が低下している状態です。
例えば、工具が所定の場所になく毎回探し回る、パソコンが遠くて入力のたびに席を移動するといった事例が挙げられます。
このような無駄は作業効率を悪化させるだけでなく、疲労やヒューマンエラーのリスクを高める原因にもなります。
無駄な動作を減らすには、作業スペースのレイアウト改善や、5S(整理・整頓・清掃・清潔・しつけ)の徹底が有効です。
不良を作る無駄
不良を作る無駄は、品質の不備によって手直し・再製作・廃棄といった追加対応が必要になることで発生します。
不良が多いと納期の遅延やクレームの発生、企業の信用低下といった深刻な問題にもつながりかねません。
具体的には、作業指示の伝達ミスや図面の読み間違いにより、大量の製品を作り直さないといけないケースなどが該当します。
この無駄を防ぐには、作業標準の整備やチェック体制の強化、原因分析に基づく再発防止策の実行が求められます。
リーン生産方式を導入するメリット
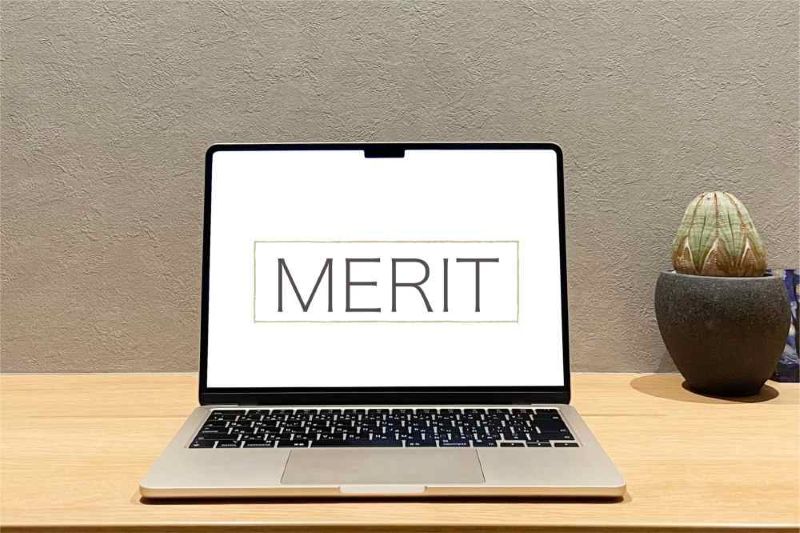
リーン生産方式は単なる生産手法ではなく、企業全体のパフォーマンスを底上げする考え方です。
無駄の排除や工程の効率化を通じて、コスト削減や品質向上といった多くの恩恵をもたらします。
ここでは、導入によって得られる6つの主なメリットを具体的に解説していきます。
無駄の排除によるコスト削減ができる
リーン生産方式では業務プロセス全体に潜む無駄を可視化し、体系的に排除していくことでコスト削減を図ります。
作業の重複や過剰な在庫、人員やエネルギーの無駄遣いを削減することで、直接費だけでなく間接費も大きく圧縮可能です。
また、継続的なコスト改善サイクルが構築されるため、一時的な削減に終わらず持続的なコスト競争力の維持にもつながります。
生産フローの改善ができる
リーン生産方式は製品やサービスが顧客に届くまでのプロセスを全体最適で捉え、各工程の無駄や停滞、バラつきを排除することに力点を置いています。
これにより、生産ラインや業務フロー全体のスピードと安定性が高まり、供給体制の強化につながります。
また、工程ごとの責任や役割も明確になり、部署をまたいだ連携やコミュニケーションも円滑になる点もメリットの1つです。
品質向上が期待できる
リーン生産方式では「最初から正しくつくる」「不良を出さない仕組みを作る」という考え方を重視しており、その結果として品質向上が実現されます。
標準作業の整備や工程内品質管理、フィードバックの仕組みを整えることにより、ばらつきやミスが起こりにくくすることが可能です。
また、問題が発生しても原因分析や再発防止が迅速に行われる文化が醸成され、品質面での継続的改善も進みます。
品質の安定は顧客満足や企業の信頼性向上にも直結する重要な要素です。
リードタイム短縮と顧客満足度向上につながる
無駄を減らし、工程を円滑にすることで、受注から納品までにかかるリードタイムを大幅に短縮できるのがリーン生産方式の大きなメリットの一つです。
これにより、顧客からの要望に迅速かつ柔軟に対応できる体制が整い、満足度や信頼性の向上につながります。
加えて、需要の変化に対するレスポンスが早くなれば、市場競争力の強化にもつながります。
従業員エンゲージメント向上が期待できる
リーン生産方式の実践においては、現場の気づきや改善提案が重要な役割を果たします。
そのため、現場の声が尊重される文化が醸成され、従業員一人ひとりが組織の一員として貢献している実感を持ちやすくなります。
このような環境では、モチベーションの向上だけでなく、チームワークや自律的な行動が促進され、結果として従業員のエンゲージメントを高めることが可能です。
従業員エンゲージメントが向上すれば、離職率の低下や組織力の強化も期待できます。
環境対応への貢献につながる
リーン生産方式は、必要以上の資源を使わず、最大の価値を生み出すことを目指す考え方です。
これにより、エネルギー使用量や廃棄物、二酸化炭素排出量などが抑えられ、環境負荷の軽減に直結します。
また、循環型社会や脱炭素といった社会的な要請にも対応できる取り組みとして、企業のESG対応やSDGs貢献の一環にも位置づけられます。
持続可能な経営を実現するうえで、リーン生産方式の導入は有効な手段です。
リーン生産方式のデメリット
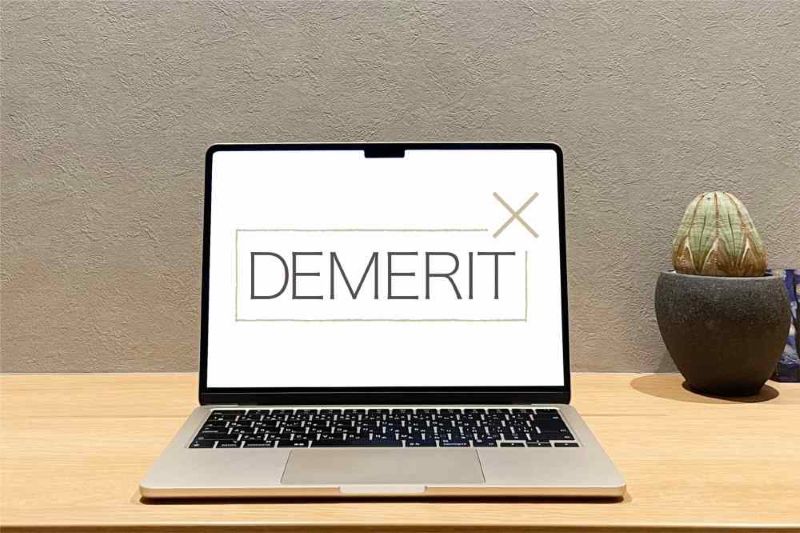
リーン生産方式は多くのメリットを持つ一方で、導入や運用において注意が必要な点も存在します。
ここでは、主なデメリットについて詳しく解説します。
精度の高い需要予測が必要
リーン生産方式では、できるだけ無駄をなくすために、あらかじめ必要なものを必要な分だけ準備して生産する考え方が基本となっています。
そのため、お客さまからの注文数や売れ行きを正確に予測することがとても重要です。
もし予測が外れてしまうと、材料が足りずに製品が作れなかったり、納期に間に合わなかったりすることがあります。
日頃からデータを集めて分析し、予測の精度を高める工夫が大切です。
導入の初期コストが高い
リーン生産方式を組織に根付かせるには、工程の見直しやレイアウトの再構築、人材教育、システム整備など、多方面にわたる初期投資が必要です。
単に設備を導入するだけでなく、現場の意識改革や全社的な体制づくりも求められるため、導入初期は時間と費用の両面でコストがかかります。
また、導入初期では一時的に業務効率が落ちることも想定され、短期的な成果が見えづらい点にも注意が必要です。
そのため、中長期的な視野で効果を評価する姿勢が求められます。
柔軟性に欠けるリスクがある
リーン生産方式は効率性と標準化を重視するため、突発的な変化や例外対応には弱い側面があります。
変化の激しい市場やカスタマイズ要素の多い製品を扱う現場では、あらかじめ決めた工程や生産計画では柔軟に対応できない場面も想定されます。
過度に効率化を進めた結果、少量多品種や個別対応への反応力が落ちる場合があることにも注意が必要です。
安定した需要を前提とする設計になりがちなため、変動への耐性を確保する仕組みも同時に検討する必要があります。
在庫管理が煩雑になりやすい
リーン生産方式では在庫をできるだけ持たないことが理想とされていますが、その分、在庫の量や動きを細かく把握し続ける必要があるため、現場には大きな負担がかかります。
最小限の在庫で運用する場合、わずかな誤差でも生産が止まるリスクが高くなり、調整や発注のタイミングも頻繁に見直さなければなりません。
また、取引先や外注先とタイミングを合わせて連携を取る場面も増え、情報共有の重要性が高まります。
在庫を切らさず、過剰にもしないためには、制度と現場の運用力を両立させる仕組みが不可欠です。
リーン生産方式を理解して業務効率化を目指そう
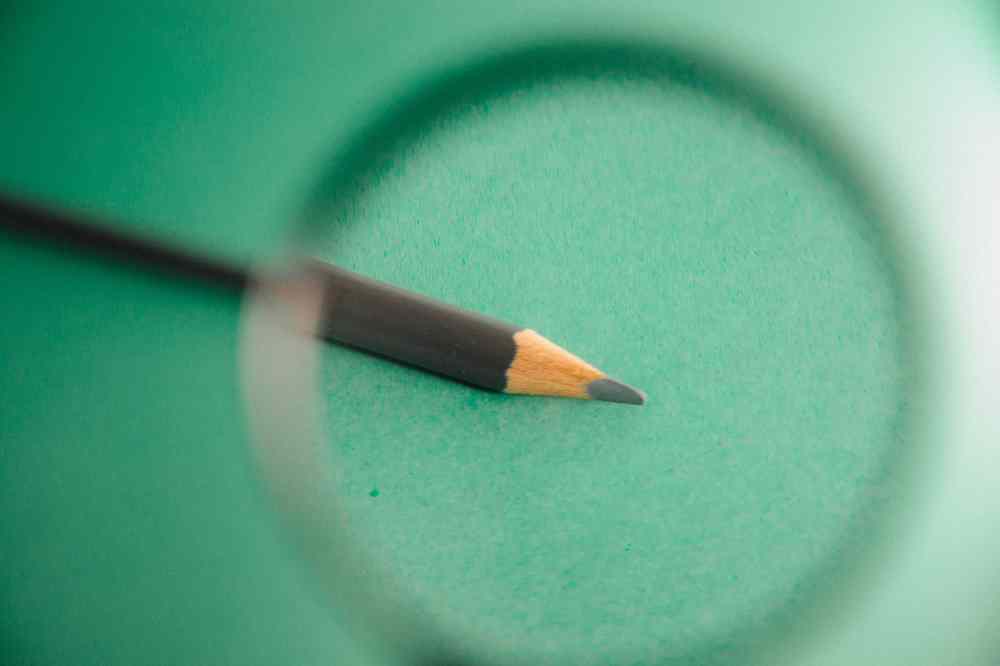
リーン生産方式は、無駄を徹底的に排除しながら価値ある工程に集中することで、生産性や品質を高める考え方です。
トヨタ生産方式を基に発展し、製造業のみならず、さまざまな業種に応用可能な考え方として広く活用されています。
基本原則や7つの無駄、メリット・デメリットを理解したうえで、自社に適した改善手法を選定することが重要です。
おすすめのお役立ち資料はこちら↓

個別受注生産の製造業向け 生産性UPを低下させる要因・対策の指南書です!
工場の生産性を上げる 6つの取り組み
~時代に合わせて成長し続ける工場へ~
