製造業における課題解決の新たな切り口として、「新QC7つ道具」があります。
従来の数値データ分析だけでは対応が難しい顧客ニーズの把握や部門間連携など、複雑化する製造現場の課題に対して、より包括的なアプローチが特徴的な手法です。
本記事では、製造業の経営層・管理職の皆様に向けて、新QC7つ道具の基本概念から実践的な活用方法まで、わかりやすく解説します。
従来のQC7つ道具との違いを踏まえながら、各手法の特徴と具体的な活用事例を見ていきましょう。
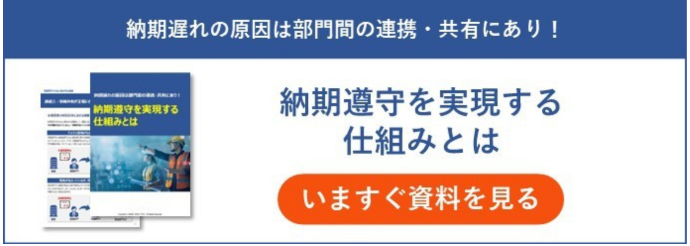
目次
製造業における新QC7つ道具とは
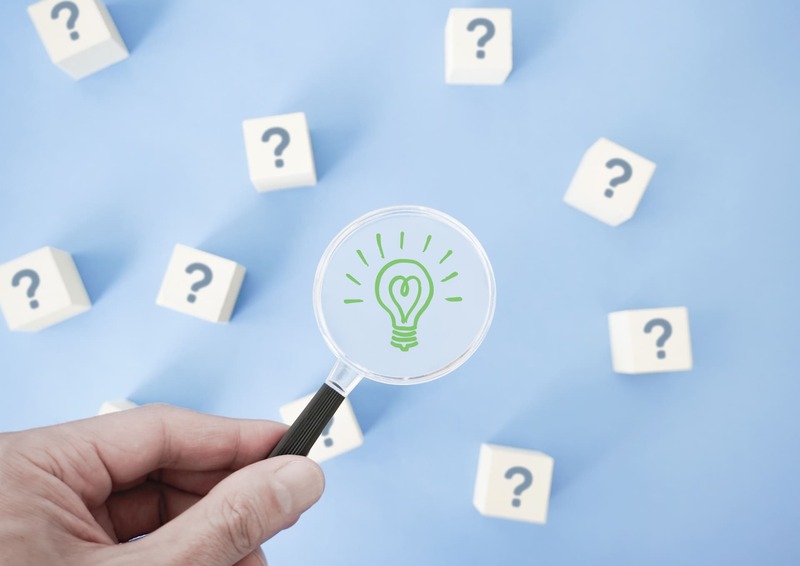
新QC7つ道具は、品質管理の概念を拡張し、定性的な情報を図解などで整理する手法です。
製造業において品質管理(QC:Quality Control)は、製品の高品質化と生産性向上に不可欠な取り組みです。
現代の製造現場では、従来の数値データだけでなく、顧客ニーズや従業員の声といった定性的な情報の分析も重要性を増しています。
新QC7つ道具は製造現場での品質管理はもちろん、商品企画や設計プロセス、さらには経営戦略の立案においても活用されています。
特に非数値データを図解や構造化によって整理・分析することに適しているため、数値化が難しい現場の課題や部門横断的な問題を整理して解決する手段として用いると効果的です。
複雑な問題を構造化し可視化することで、より効率的な問題解決を実現できます。
新QC7つ道具一覧
新QC7つ道具は、製造業の品質改善活動において欠かせない7つの分析手法で構成されています。
具体的には、以下の7つの手法です。
- 親和図法:アイデアや意見を似た内容ごとにまとめ、問題の全体像を把握
- 連関図法:課題間の因果関係を矢印で結び、複雑な問題構造を可視化
- 系統図法:目的達成のための方策をツリー構造で体系的に整理
- アローダイアグラム法:プロジェクトの進行過程を時系列で管理
- マトリックス図法:2つの要素群の相関関係を表形式で分析
- マトリックスデータ解析法:多変量データの相関性を統計的に分析
- PDPC法:目標達成までのプロセスと起こりうる問題点を予測
また、これらの手法は、以下のように「新連携アロマでP」という語呂合わせで覚えることができます。
- 新:親和図法
- 連:連関図法
- 携:系統図法
- アロ:アローダイヤグラム法
- マ:マトリックス図法
- で:データ解析法
- P:PDPC法
各手法は単独でも使用可能ですが、複数を組み合わせることでより効果的な問題解決が可能です。
従来のQC7つ道具一覧
従来のQC7つ道具は、製造現場で発生する品質や工程に関わる数値データを整理・分析するための統計的品質管理手法です。
この手法は、主に数値データを基に問題の特定や改善を行うことを目的としており、製造工程での現状把握や品質維持に欠かせません。
これらの手法は、以下の7つで構成されています。
- 散布図:2つの要素の相関関係を視覚化するグラフ
- チェックシート:データを収集し、点検や確認を体系的に行うための一覧表
- 管理図:工程が管理限界内に収まっているかを判定するための図表
- 特性要因図:問題の原因を階層的に整理し、可視化するための図
- ヒストグラム:データの分布状況を直感的に把握する棒グラフ
- パレート図:問題や原因を重要度順に整理し、効果的な対応を促すグラフ
- グラフ:傾向や変化を視覚的に示すための汎用的な手法
これらの手法は、「サンチェ監督引っ張れそう」という語呂合わせで覚えることができます。
- サン:散布図
- チェ:チェックシート
- 監:管理図
- 督:特性要因図
- 引:ヒストグラム
- っ張れ:パレート図
- そう:層別・グラフ
製造プロセスの現状把握、課題発見、要因特定、効果確認など、各フェーズで適切に活用することで、データに基づいた意思決定と継続的な改善活動に役立ちます。
新QC7つの道具と従来のQC7つ道具の違いとは
新QC7つの道具と従来のQC7つ道具は、どちらも品質管理における重要な手法ですが、主に扱うデータの種類や活用範囲、目的に違いがあります。
これらの特徴を正確に理解することで、状況に応じた適切な手法を選択し、問題解決の効率を高めることが可能です。
従来のQC7つ道具 |
新QC7つ道具 |
|
扱うデータ |
定量的(数値)データ |
定性的(言語)データ |
適用範囲 |
主に製造現場 |
製造現場、企画、設計、営業、総務など多部門で活用可能 |
評価の特徴 |
客観的かつ明確な評価が可能 |
主観的な内容も整理し、分かりやすく可視化 |
活用目的 |
不良率や稼働率の改善などの数値データ分析 |
数値化が難しい問題や複雑な課題の構造化と解決策の創出 |
使用場面 |
数値データを取得できる製造業や販売業 |
サービス業や介護業など、数値化が難しい業種にも対応 |
具体的な活用シーンの違い
従来のQC7つ道具
従来型は、不良率や稼働率といった具体的な数値を基にした品質の改善を重視しています。
統計的手法を活用し、製造現場での定量的な問題解決に特化しています。
新QC7つ道具
一方、新QC7つ道具は、漠然とした問題や数値化できない課題を可視化し、解決策を導くプロセスに適しています。
また、部門横断的なプロジェクトや、サービス業のように数値だけでは把握できない業務課題にも対応可能です。
両者は対立するものではなく、目的や状況に応じて相互補完的に使い分けることが最も効果的です。
例えば、製造現場では従来のQC7つ道具を用いて数値を分析し、新QC7つ道具を活用して課題を整理・解決する、といった運用が効果的です。
新QC7つ道具の手法と活用事例

新QC7つ道具は、製造業における問題解決と品質改善に欠かせない手法です。
これらの手法は、複雑な課題を体系的に整理し、効果的な解決策を導き出すのに役立ちます。
新QC7つ道具の手法について、その特徴と活用事例を詳しく解説します。
親和図法
親和図法は、製造業における複雑な問題を整理し、解決の糸口を見出すために使用される手法です。
親和図法の特徴は、バラバラな情報やアイデアを体系的にグループ化し、問題の全体像を可視化できる点にあります。
具体的な活用例として、新製品開発のプロセスを考えてみましょう。
経営層の皆様が、市場ニーズに応える革新的な製品を生み出したいと考えた場合、親和図法を用いて次のように進められます。
- 顧客の声、市場調査データ、技術者のアイデアなどを個別のカードに記入
- これらのカードを類似性に基づいてグループ化
- グループごとにタイトルをつけ、全体の構造を把握
この過程を通じて、例えば「省エネ性能の向上」「操作性の改善」「デザインの刷新」といった主要なテーマが浮かび上がってくるでしょう。
これにより、開発の方向性が明確になり、限られたリソースを効果的に各プロジェクトに配分することが可能です。
また、親和図法は、品質改善や現場の問題解決にも応用できます。
不良品発生の原因分析や生産効率向上のためのアイデア出しなど、現場の声を効果的に集約し、経営層の意思決定に活かすことが可能な手法です。
連関図法
連関図法は、製造現場における複雑な課題の因果関係を視覚的に明確化する手法です。
連関図法は、問題の構造を網目状に表現することで、複雑に絡み合った要因を整理し、重要な改善ポイントを特定できます。
製造業においては、以下のような品質管理や生産性向上で活用されている手法です。
- 不良品発生メカニズムの解明
- 品質低下要因の相互関係分析
- 改善施策の影響範囲把握
- 生産遅延の要因分析
- 設備稼働率向上の要因把握
また、連関図法は以下のような手順で作成できます。
- 中心テーマの設定(例:不良率上昇)
- 関連要因の洗い出し
- 要因間の関係性を矢印で表現
- 影響度の強い要因を特定
連関図法は、製造現場の課題を構造的に理解し、戦略的な意思決定を行うことが可能です。
特に、複数の部門が関わる横断的な問題解決において効果を発揮します。
系統図法
系統図法は、製造業における目標達成のための具体的な実行計画を体系的に整理する手法です。
目的から手段へと階層的に展開することで、抽象的な目標を具体的なアクションプランへと落とし込むことができます。
例えば、製造業における品質向上において階層的に展開すると以下のようになります。
- 目的:不良率50%削減
- 一次手段:検査強化、作業環境改善、教育訓練
- 二次手段:検査項目見直し、温湿度管理、技能認定制度
系統図法を作成するポイントは、以下の3点です。
- 明確な目標設定
- 実現可能な手段への展開
- 具体的なアクションプランの策定
系統図法は、戦略的な目標を現場レベルの具体的な施策へと展開する際の効果的な手段となります。
中長期的な経営計画の立案や全社的な改善活動の推進において特に有効です。
アローダイアグラム法
アローダイアグラム法は、プロジェクトの作業工程を矢印と結合点で示し、最適なスケジュールを立案する手法です。
作業の前後関係や所要時間を可視化し、全体像を把握しながら進捗を管理できます。
例えば、新製品開発プロジェクトでは、設計から量産までの工程管理や部門間の連携スケジュール調整などを可視化し、全体像を把握するために活用されます。
アローダイアグラム法の作成手順は、目的の設定→主要作業の洗い出し→所要時間の設定→アローダイアグラムの作成という流れです。
矢印が作業の順序を示し、ノード(結合点)が作業そのものを表します。
プロジェクト全体の進捗を一目で把握できるため、計画段階から確実な工程管理を実施しやすくなります。
マトリックス図法
マトリックス図法は、2つの要素を行と列に配置し、交点で関連度合いを示す手法です。
製造現場で扱う複雑な情報を整理する際、視覚的な配置によって重要項目を見落としにくくする役割を担います。
マトリックス図法がもたらす利点には、不良原因と対策の関連度を可視化し、改善施策における優先度を明確にできる点が挙げられます。
さらに、行と列を掛け合わせて数値評価を行えば、客観的な検討がしやすいでしょう。
下記は、マトリックス図法を活用した一例です。
行には「改善案」、列には「コスト」「作業負荷」「生産性向上度」を設定し、交点は記号で関連度を示しています。
コスト |
作業負荷 |
生産性向上度 |
|
改善案A |
◎ |
△ |
○ |
改善案B |
○ |
◎ |
◎ |
改善案C |
△ |
○ |
△ |
記号の種類や評価基準については、社内の目的や基準に合わせて設定できます。
例えば、◎を「高い」、○を「中」、△を「低い」というように定義すると、優先的に取るべき施策を客観的に検討しやすくなります。
マトリックス図法は、投資対効果の分析や改善施策の優先順位付けなど、戦略的な意思決定を支援する有効な手段です。
マトリックスデータ解析法
マトリックスデータ解析法は、多数の数値を整理し、相関を可視化することで最適な意思決定を支援する分析手法です。
従来の新QC7つ道具の中では、珍しく定量データに焦点を当てる点が特徴的です。
例えば、製造工程で取得した複数の品質指標を総合的に分析し、どの要素が不良率や歩留まりに強く影響するかを把握できます。
製造業での具体的な活用例として、生産設備の稼働状況を複数項目(稼働時間、消費電力、歩留まりなど)で評価し、主要な改善ポイントを抽出するケースが挙げられます。
さらに、工程間で取得したデータを一括で解析し、工程設計や保全計画の優先度を検討する際にも効果的です。
下記は、生産ラインをまとめたマトリックスデータ解析の参考例です。
評価項目 |
ライン1 |
ライン2 |
ライン3 |
生産性指標 |
92 |
85 |
88 |
品質スコア |
88 |
93 |
85 |
エネルギー効率 |
85 |
90 |
92 |
メンテナンス性 |
90 |
87 |
86 |
各項目の相関を数値化することで、重要度の高い領域を可視化でき、経営戦略や製造現場の改善施策の優先度を判断しやすくなります。
PDPC法
PDPC法(Process Decision Program Chart)は、製造現場における目標達成までのプロセスで発生し得るリスクを事前に予測し、その対策を体系的に整理する手法です。
製造業特有の予期せぬトラブルに対して、迅速かつ適切な対応を可能にします。
PDPC法には、以下の2つの主要タイプがあります。
- 強制連結型:計画時に不測の事態を予測し、必ずゴールまでの経路をつなぐ
- 逐次展開型:問題発生時に都度対策を考え、計画を修正しながら進める
状況に応じて使い分けすると、複雑な事態の経緯を一望でき、さらに独断と偏見を排除できる対策を図式化できます。
新製品立ち上げにおける量産開始時のトラブル予測や品質基準未達時の対応策などPDPC法を活用することで迅速な対応が可能です。
PDPC法を活用すれば製造実務におけるリスク管理を体系的に行い、迅速な対応力の向上が期待できます。
また、経営層が戦略的に使うことでトラブル対応の負担を減らし、最終的なコストパフォーマンスの向上にもつながります。
新QC7つ道具を効果的に活用するための注意点
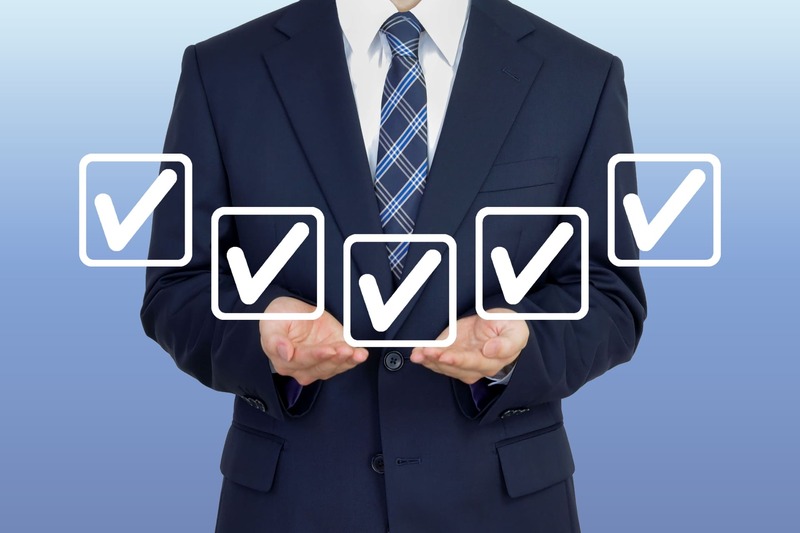
新QC7つ道具は、製造業の改善活動において効果的な手法として機能しますが、いくつかの重要な注意点があります。
これらの注意点を意識することで、より確実な問題解決と改善活動の推進が可能です。
以下の3つのポイントについて、詳しく見ていきましょう。
- 解決したい問題に適した手法を選ぶこと
- 目的に応じて複数の手法を組み合わせて活用すること
- 特定個人の意見に偏らないよう配慮すること
解決したい問題に適した手法を選ぶこと
効果的な問題解決には、課題の性質を見極め、最適な手法を選択することが重要です。
例えば、複数の意見やアイデアを整理する場合は親和図法、因果関係を明確にしたい場合は連関図法というように、状況に応じて使い分けることで成果が高まります。
製造現場では、品質改善や工程改革など、様々な課題に直面します。
これらの問題に対して、以下の観点から最適な手法を選択することをおすすめします。
- 問題の性質(定性的か定量的か)
- 求める成果(アイデア創出か構造化か)
- 参加者の経験レベル
- 利用可能な時間と資源
これらの要素を考慮しながら、現場に適した手法の選定を指導して、より効果的な改善活動を推進しましょう。
目的に応じて複数の手法を組み合わせて活用すること
製造業における複雑な課題解決には、複数の手法を組み合わせた段階的なアプローチが効果的です。
例えば、品質改善プロジェクトでは、まず親和図法で問題点を整理し、次に連関図法で原因を分析、さらに系統図法で具体的な対策を検討するといった流れで進めます。
各手法には得意分野があり、それらを相互補完的に活用することで、より確実な成果につながります。具体的な組み合わせ例は、以下の通りです。
- 課題抽出:親和図法
- 要因分析:連関図法
- 対策立案:系統図法
- 実行計画:PDPC法
このように、問題解決の各段階で適切な手法を選択し、組み合わせることで、より効果的な改善活動が実現できます。
特定個人の意見に偏らないよう配慮すること
製造現場の改善活動において、特定個人の意見や解釈に偏ることは、本質的な問題解決の妨げとなります。
新QC7つ道具は、言語データを扱うため、個人の主観が入りやすい特徴があります。
そのため、以下のような取り組みが重要です。
- チーム全体での議論促進
- 現場作業者から管理者まで幅広い意見収集
- 部門を超えた多様な視点の取り入れ
- 客観的な分析の実施
- データに基づく事実確認
- 複数メンバーでの検証
経営層が多様な意見を尊重し、バランスの取れた改善活動を推進することで、より効果的な問題解決が実現できます。
新QC7つ道具を活用し製造マネジメントを確立しよう
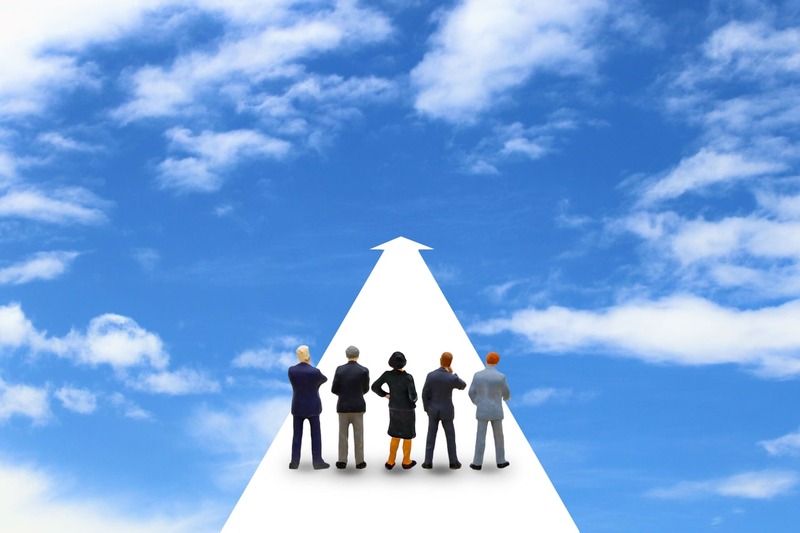
新QC7つ道具は、製造業における品質改善と問題解決の強力な手法です。
新QC7つ道具を活用した製造マネジメントの確立は、品質向上、コスト削減、そして顧客満足度の向上につながります。
しかし、製造マネジメントの確立には、新QC7つ道具の活用だけでなく、部門間の連携や情報共有も重要です。
特に個別受注生産においては、納期遵守が大きな課題といえます。
この課題に対する具体的な解決策について、より詳しく知りたい方は、「納期遵守を実現する仕組みとは」という無料資料をぜひご覧ください。
この資料では、納期遅れの根本的な原因と、それを解決するための実践的な方法を詳しく解説しています。
製造マネジメントのさらなる向上にお役立てください。
おすすめのお役立ち資料はこちら↓
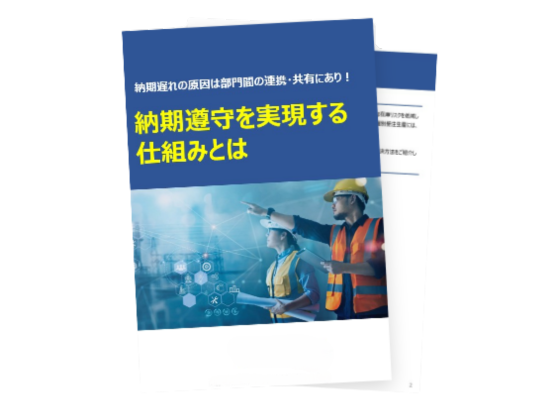
納期遅れの原因は部門間の連携・共有にあり!
納期遵守を実現する仕組みとは
