製造業や生産管理に携わる中で、「MPSとは何か」「MRPとの違いがよくわからない」と悩んでいる方も多いのではないでしょうか。
MPSとMRPは生産計画の要ですが、両者の違いや連携方法を理解していないと、計画のズレや在庫管理の失敗を引き起こす原因にもなります。
本記事では、MPSの基本からMRPとの違い、そしてMPSを活用するメリットを徹底的に解説します。
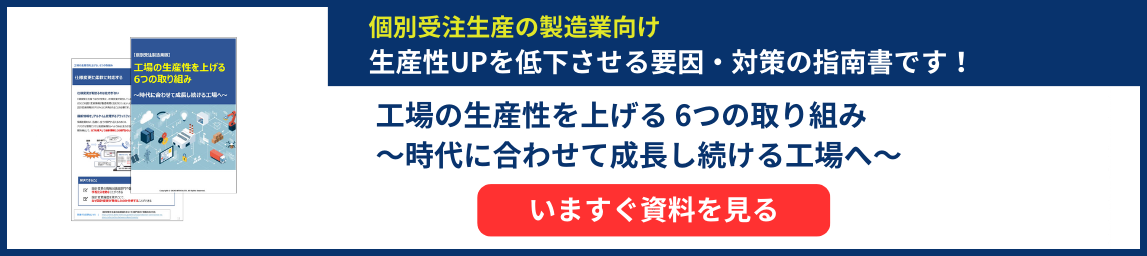
目次
MPS(基準日程生産計画)とは

MPSとは「基準日程生産計画」とも呼ばれ、需要予測や受注情報に基づいて、どの製品を・どのタイミングで・どれだけ生産するかを計画する仕組みです。
MPSは生産活動の最初の基準となるため、後工程である資材調達や詳細スケジューリングの土台になります。
特に、MRP(資材所要計画)との違いや関係性を正しく理解することで、生産計画の精度や柔軟性が大きく向上します。
MPSとMRPの違い
MPSとMRPはどちらも生産計画に関わる仕組みですが、その役割は明確に異なります。
MPS |
MRP |
|
対象 |
完成品(製品レベル) |
部品・資材(構成品レベル) |
主な目的 |
何を・いつ・どれだけ作るかを決める |
何を・いつ・どれだけ手配するかを決める |
MPSは「何を・いつ・どれだけ作るか」という製品レベルのスケジュールを決める上位計画で、完成品の計画にフォーカスしています。
一方でMRPは、MPSの結果を基にして「必要な部品や資材を、いつ・どれだけ手配するか」を決める仕組みです。
両者を混同すると、手配の遅れや在庫の過不足が発生しやすくなるため、それぞれの役割分担を正しく理解することが重要です。
MRPについてさらに詳しく知りたい方は下記をご覧ください。
MRP(資材所要量計画)をわかりやすく解説!製造業の競争力を高める戦略的ツール
MPSが重要とされる理由
MPSが重視される理由の一つは、生産の安定性を保ちながら効率を高めるための「軸」になるという点です。
もしMPSがなければ、各部門がバラバラに動き、過剰在庫や部品不足などのトラブルが発生しやすくなります。
また、MPSを用いることで需要変動にも柔軟に対応できるようになり、製造ラインの混乱や無駄なコストの発生を回避することが可能です。
特に変化の激しい現代の製造現場では、精度の高い中期的な指針を持つことが企業の競争力にも直結します。
MPSがしっかりしているほど、全体の生産性や顧客満足度も高まりやすくなります。
MPSとMRPの連携の重要性
MPSとMRPは単体で機能させるのではなく、密接に連携させることで最大の効果を発揮します。
MPSが立てた製品の生産スケジュールに基づいて、MRPが部品や原材料の調達を管理する流れになっているため、MPSがズレてしまえば、MRPも正しく機能しなくなります。
例えば、MPSで来週100台生産する予定だった冷蔵庫が急遽150台に変更された場合、MRPがそれに気づかず従来通りの材料を発注していたら、不足が起こり納期遅れにつながりかねません。
逆に、MPSが不確かなままMRPが正確に動いても、在庫過多や資材の無駄が発生してしまいます。
このような事態を避けるには両者の計画がシステム上でしっかりと連携し、変更時にもリアルタイムで情報が反映される体制が重要です。
MPSを活用するメリット

MPSを導入することで得られるメリットは、単にスケジュールを決めるだけにとどまりません。
現場での生産負荷の調整や在庫の最適化、全体のコスト削減など多くの利点があります。
ここでは、MPSを活用するメリットについて詳しく解説します。
生産負荷の平準化と需給変動への柔軟対応
MPSを活用すると、工場の生産負荷を一定に保ちやすくなります。
これは「平準化」と呼ばれ、忙しい時期とそうでない時期の差を小さくすることで、安定した生産が可能です。
また、MPSでは予め需要予測に基づいて生産スケジュールを立てるため、急な注文があったときにも柔軟に対応しやすくなります。
結果として、納期遅れのリスクを下げたり、従業員の負担を軽減できたりするのがメリットです。
生産負荷を平準化することで品質も安定し、全体の業務もスムーズに回りやすくなります。
生産リソースの最適活用と在庫の適正化
MPSを活用することで、工場の設備や人手、材料といった生産リソースを無駄なく使えます。
予め生産内容やスケジュールが明確になるため、どの作業をいつ実施するのかを効率的に組み立てることが可能です。
これにより、使われていない設備の待機時間を減らしたり、必要な人員を的確に配置できたりと、全体の稼働効率向上が期待できます。
さらに、材料の使用量やタイミングを事前に把握できるため、在庫を必要最小限に抑えることも可能です。
在庫量が適正化されることで、保管スペースの圧迫や過剰在庫による廃棄といった問題も発生しにくくなり、安定した生産体制の維持につながります。
生産効率向上によるコスト削減と利益改善
MPSを導入することで、無駄のない計画が立てられるようになり、生産効率が大きく向上します。
計画通りに作業を進められれば、急な残業や突発的な人員追加が不要となり、コストの増加を抑えることが可能です。
また、在庫を必要以上に抱えることもなくなるため、保管費用の削減にもつながります。
さらに、作業の無駄をなくすことで、製造にかかる時間や材料のロスも減少します。
このような積み重ねにより、全体のコストが見直され、結果として利益の改善が期待できるようになるのです。
効率の良い生産体制は、企業の競争力向上にも寄与するため、長期的な経営戦略としても重要な意味を持ちます。
MPSの主な機能

MPSは、生産活動全体の基盤となる役割を持ちます。
その中でも特に重要なのが「需給計画」と「生産計画」の2つの機能であり、これらを通じて効率的で無駄のない生産体制の構築が可能になります。
以下で詳しく見ていきましょう。
需給計画
需給計画とは、製品の「需要(お客さまからの注文や予測)」と「供給(在庫や生産能力)」のバランスを取るための計画です。
例えば、来月に注文が100個入ると予測されている場合、現在の在庫が20個であれば、残り80個をいつまでに生産・調達するかを考えます。
このように、需給計画は足りないものを見える化し、過剰にならないようにするために欠かせない計画です。
また、需給計画を基に資材の手配も行われるため、MRPとも密接に関係しています。
MRPが部品や材料レベルの計画なのに対し、MPSは完成品レベルの計画なので、会社全体の動きを見ながら判断する点が特徴です。
このように、需給計画は企業の生産と販売をつなぐ架け橋として、非常に重要な役割を担っています。
生産計画
生産計画は、需給計画に基づいて「具体的にどの製品を、いつ、どのラインで、どれだけ作るか」を決める工程です。
単に数量を決めるだけでなく、生産リードタイム(製品が完成するまでの期間)や設備の空き状況、人員の配置なども加味してスケジューリングします。
例えば、Aという商品を月曜に100個、火曜に150個作る必要があるとわかったら、それに合わせて原料の準備や機械の稼働時間、人手の手配を行います。
この調整がうまくいくことで、無駄な待ち時間や手戻りを減らし、全体の生産効率を上げることが可能です。
また、生産計画は中長期的な視点だけでなく、日々のオペレーションにも直結するため、急な注文変更やトラブルに柔軟に対応できるような姿勢も求められます。
生産計画の立て方

生産計画は、製品をスムーズに作るための土台となる作業です。
特にMPSでは、時間の長さによって「大日程(長期)」「中日程(中期)」「小日程(短期)」の3つのステップに分けて計画を立てていきます。
以下で詳しく解説します。
ステップ① 大日程計画(長期計画)の作成
大日程計画は、3カ月から1年先を見据えてどの時期にどれだけの需要があるかを大まかに把握するための計画です。
これは企業全体の経営戦略や販売予測と結びついており、「どの工場でどの商品を作るか」「新製品をいつ市場に出すか」といった判断にも影響します。
大日程計画ではリスクを見越して早めに動くことが大切です。
この段階では詳細なスケジュールまでは詰めませんが、方向性を決めておくことで、後の計画づくりがスムーズになります。
ステップ② 中日程計画(中期計画)の作成
中日程計画は、1カ月から3カ月程度の期間を対象にして、どの週に何をどれだけ生産するかを具体的に決める作業です。
ここでは、販売部門や調達部門と連携しながら、生産ラインの稼働率や人員配置、材料の調達計画などを考慮します。
例えば、特定の週に受注が集中している場合は、その週に向けて生産ラインの稼働を調整する必要があります。
逆に需要が少ない週はメンテナンスや教育などに充てることも可能です。
中日程計画では、過去の実績や販売動向に基づいて現実的な数字を出すため、データ分析の力が求められます。
柔軟に対応できる余地を残しながら、無駄のないスケジュールを組むことがポイントです。
ステップ③ 小日程計画(短期計画)の作成
小日程計画は、1週間から日単位、時には時間単位で「いつ、どこで、誰が、どの機械を使って、何を作るか」を決める最も具体的な工程です。
現場オペレーションと直結しており、実際の生産活動に大きな影響を与えるため、計画精度が重要になります。
また、急なトラブルや注文変更にも対応できるよう、予備時間やバックアップの考慮も不可欠です。
小日程計画は現場との密な連携が求められるため、コミュニケーションや進捗確認も重要な業務となります。
生産管理におけるMPS活用の課題

MPSは生産計画の中核を担う仕組みですが、運用にはさまざまな課題が存在します。
特に「柔軟性の低さ」「データの正確性」「システムの制約」の3点は、多くの現場で悩まれている共通のテーマです。
これらの壁をどう乗り越えるかが、MPSをうまく生かす鍵となります。
計画の柔軟性不足と生産能力の限界
MPSは長期的な生産計画を立てるうえで有効ですが、計画が一度決まってしまうと、現場での急な変更に対応しにくいという弱点があります。
また、生産設備の能力にも限界があるため、計画通りに進めようとしても実際には人手や機械の稼働時間が足りないといった問題が発生する場合も少なくありません。
こうした状況では計画と実行の間にギャップが生まれやすく、結果的に納期遅延や品質の低下を招くリスクが高まります。
そのため、MPSを運用する際には変化に強い仕組みを構築し、現場との連携を密にしておくことが重要です。
データ精度の問題と属人化リスク
MPSの計画精度は、基になるデータの正確性に大きく依存します。
しかし実際には販売予測や在庫数、リードタイムなどの情報が不正確なまま入力されているケースも少なくありません。
こうした誤差が積み重なると、計画そのものが現実離れしたものになり、結果として混乱を引き起こします。
また、計画立案や調整業務が特定の担当者に偏っている場合、その人が不在になったときに対応できない「属人化リスク」も大きな問題です。
ブラックボックス化した運用は、引き継ぎの難しさや業務効率の低下につながる可能性があります。
この課題を解決するには、データの標準化と見える化、そして業務フローのマニュアル化が必要不可欠です。
ERPや生産管理パッケージの制約と対応策
MPSを活用するには、ERP(企業資源計画)や生産管理システムとの連携が欠かせません。
ERPとは、販売・在庫・購買・会計など、企業の基幹業務を統合的に管理できるシステムのことです。
しかし、実際の運用現場では「システムの機能が足りない」「操作が複雑で現場に浸透しない」といった制約に悩まされることがあります。
特に中小企業では、自社の業務フローに合わない既製品のシステムを使っているケースも多く、現場での活用が定着しにくい状況が見受けられます。
また、システム導入時に十分なトレーニングが行われなかった場合、担当者が正しく活用できずに手作業に頼ってしまうといった問題も発生します。
その結果、せっかくのMPS機能が形だけになってしまうこともあります。
このような場合は、カスタマイズ可能なツールの導入や、段階的な教育・改善活動を取り入れることが効果的です。
MPSを成功させるためのポイント

MPSを実際に機能させ、安定した生産体制を築くには、いくつかの重要なポイントがあります。
以下で詳しく解説します。
正確な需要予測に基づく計画立案
MPSの成否は、需要予測の精度に大きく左右されます。
見込みが外れると過剰在庫や欠品につながり、無駄なコストや納期遅延が発生してしまいます。
そこで重要になるのが、信頼性の高いデータを基にした予測です。
例えば、過去の出荷実績や市場トレンド、季節要因などを統計的に分析することで、より現実的な数値を導き出せます。
販売部門やマーケティング部門と連携し、多角的な視点で予測を組み立てることもポイントです。
このように、精度の高い需要予測は、MPSの計画そのものの質を底上げする役割を果たします。
現場の実態に即した柔軟なスケジューリング
どれだけ綿密に計画を立てたとしても、現場では想定外のことが起こる場合があります。
機械の故障や人員不足、急な仕様変更など、日々の現場は変化の連続です。
そのため、MPSにおいても一定の柔軟性を持たせた構成が求められます。
具体的には、予備の時間を予め計画に組み込んだり、優先順位の高い製品から順に割り当てる方式を採用したりすることで、計画の破綻を防ぎやすくなります。
また、現場担当者との定期的なすり合わせやフィードバックの場を設けることも、柔軟な運用につながる有効な手段です。
システム連携とデータ精度の徹底管理
MPSは単体で機能するものではなく、販売管理、在庫管理、購買管理などの他システムと情報を連携させることで真価を発揮します。
特にERPやMES(製造実行システム)などとつなげることで、データの一元化とリアルタイムな計画更新が可能です。
しかし、システム連携がうまくいかないと、情報のズレや入力ミスが発生し、計画の精度が損なわれてしまいます。
そのため、マスターデータ(製品情報やリードタイムなど)の定期的な見直しや、入力ルールの整備といった運用管理が欠かせません。
また、関係部門間でのデータ共有や更新タイミングの統一など、全体最適の視点から仕組みを整えることも重要です。
MPSを理解して生産計画を最適化しよう

MPSは、製造業における安定的な生産と効率的なリソース活用を実現するための重要な仕組みです。
MRPとの違いを理解し、需要予測や現場との連携、システム活用を通じて計画の実行力を高めることが大切です。
正しく運用することで、生産計画の精度が向上し、企業全体の競争力強化にもつながるでしょう。
MPSを単なる理論で終わらせず、実務に生かす視点が今後ますます重要になります。
本記事を参考にしてMPSを上手く活用し、生産計画を最適化しましょう。
おすすめのお役立ち資料はこちら↓

個別受注生産の製造業向け 生産性UPを低下させる要因・対策の指南書です!
工場の生産性を上げる 6つの取り組み
~時代に合わせて成長し続ける工場へ~
