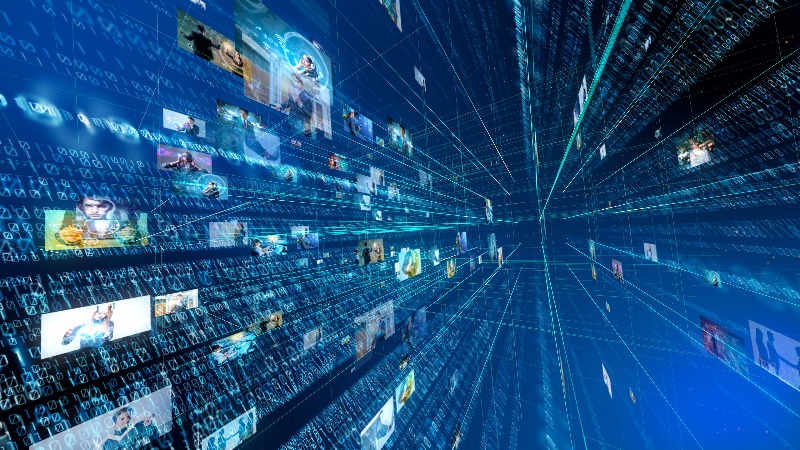
製造業の現場では保守や保全といった言葉がよく聞かれます。しかし、よく似た意味合いを持つこれらの言葉の違いをはっきりと説明できる方は少ないのではないでしょうか。
本記事では、保守と保全の違いや保全業務の実施における重要事項について解説します。
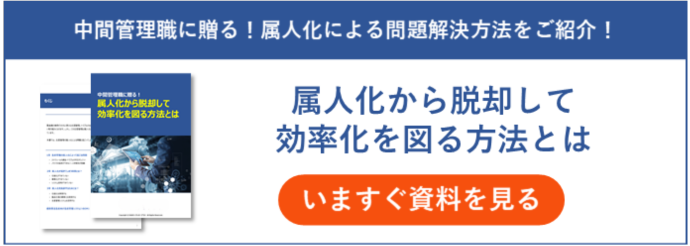
目次
製造業における保全とは?保守との違いも解説
製造業などで多く用いられている言葉の中に「保全」や「保守」といったものがあります。どちらの言葉も機械や設備を点検・修理するという共通点があることから混同されがちですが、実際には明確な違いがあります。
まず、「保全」は故障しないように前もって点検を行うことを指します。生産の安定的な稼働を実現するためのメンテナンスの意味合いが強く、定期的な点検や部品の交換を行います。
「保守」は機械や設備が故障した際に元の状態に戻すことを指します。保全が故障する前の対策である一方で、保守は故障後の対応であることから「事後保全」と呼ばれる場合もあります。
どちらも長期間にわたり設備を安全に使用し、安定した生産を行ううえで欠かせません。本記事では事前対応である「保全」に焦点を当てて解説していきます。
保守の詳細な内容は以下記事で解説していますので、ぜひご覧ください。
保全が必要な理由
製造の現場においては保守と同様に保全も必要不可欠です。仮に保全を行わないまま生産設備を稼働し続けてしまえば、生産効率が低下するだけでなく、不良品の発生や故障にともなう事故にもつながりかねません。
保全をしっかりと行うことで、これらのトラブルを未然に防止できます。万が一稼働停止となっても、最小限の被害に抑えられたり、迅速な復旧が可能になったりします。また、適切なメンテナンスが行えるため、生産設備が長寿命化することによるコスト削減も期待できます。
このように保全は製造現場で重要な役割を果たしますが、保全にはいくつかの種類が存在します。次章では保全の種類について解説します。
保全の2つの種類
保全は「予防保全」と「予知保全」の2つの種類に分けることができます。以下では、それぞれの違いについて解説します。
予防保全
予防保全は部品の使用回数や稼働期間などを考慮したうえで、定期的に行う保全業務のことを指します。部品が故障してから交換するのではなく、事前に定めた定期点検によって部品の状態を確認し、交換を行うため、設備の安定稼働につながります。車でいえば、カーディーラーが行う定期点検やガソリンスタンドでの日常点検が予防保全にあたります。
予知保全
予知保全は機械や設備の状態を定期的に検査して、故障や不具合の兆候が出た際に行う保全業務のことです。一見予防保全と同じに思えますが、保全のタイミングが異なります。
予防保全の場合、点検のタイミングを事前に決め、定期的に保全業務を行います。一方で、予知保全は定期的な検査をお客さまとの間で結び、「壊れる可能性がある」という兆候が出た段階で保全業務を行います。
部品の調子が偶然悪かったり、環境によって状態が悪くなったりした場合の故障は、予防保全では防ぐことが困難ですが、予知保全ならば対応することが可能です。また、まだまだ使える部品が交換されてしまうといった無駄に発生するコストを削減できます。このように予知保全は保全のタイミングとコストが適切化できる方法と言えます。
以下では予防保全・予知保全を行っていくうえで重要な仕組みを解説します。
保全業務にて重要な「履歴のデータベース化」。メリットとは?
適切な保全業務を実施していくうえでは、メンテナンス履歴をデータベース化しておくことが重要です。ここでは製造業において、履歴のデータベース化をすることで得られるメリットについて解説します。
誰でも適切な保全が行える
メンテナンスの過去実績をデータベース化していないと、どの設備にいつメンテナンスをしたのか把握しづらく、適切な保全が行えない可能性があります。
また予知保全は、わかる情報を基に兆候の察知をするため作業者の経験や知識が必要で、属人性が高い業務です。そのため、IoT機器などのセンシングとデータ分析から異常の兆候を知ることが必要です。
業務が効率化し、ミスを減らせる
表計算ソフトなどを用いて手入力でメンテナンス履歴を管理している企業は未だ多くあります。このような場合、メンテナンス後に情報の更新を忘れてしまったり、手作業の入力で手間がかかったりすることから、記入ミスや記入漏れが発生してしまい、効率的に管理できないことがあります。
また、備品管理台帳の情報とメンテナンスの内容を紐づけるのに多くの時間を要してしまうケースや、担当者毎に運用方法が異なることで後任が育成しづらいといった問題も起こります。
このような非効率さを改善し、ミスを発生させないためにもメンテナンス履歴のデータベース化が効果的です。
保守・保全業務のデータベース化については以下記事でも解説していますので、こちらもあわせてご覧ください。
メンテナンス履歴をデータベース化することで、効率的な保守・保全業務が実現できるため、新たなビジネスとしてお客さまに納品した製品の保守・保全といった価値を提供することも可能です。
次章では、履歴のデータベース化を実現するソリューションについてご紹介します。
rBOMで最適な保守・保全を
DAIKO XTECHが提供するハイブリッド販売・生産管理システム「rBOM」の保守オプションでは、保守・保全履歴のデータベース化を実現できます。
補修部品の管理も行えるため、故障しやすいパーツの改善点を発見し、製品開発のヒントとすることができます。保守の受注から見積、管理品、保守部品表、作業登録など保守に関する業務を可視化することも可能です。
また、IoTとAIを組み合わせることで、お客さまに収めた製品の稼働状況の見える化を実現します。音、熱、振動を計測し、AIが多角的に分析することで適切な保全の実現をサポートします。
rBOMの詳細および資料のダウンロードについては以下より行えますので、
適切な保守・保全を行いたい方、
自社製品の保守オプションの提供をご検討されている方はぜひご利用ください。
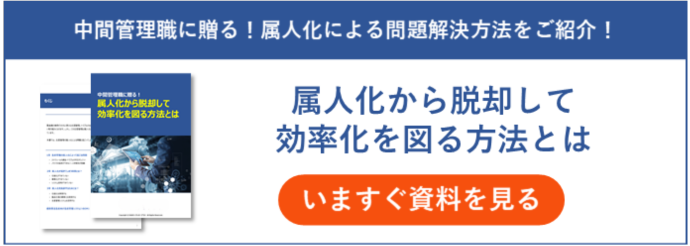
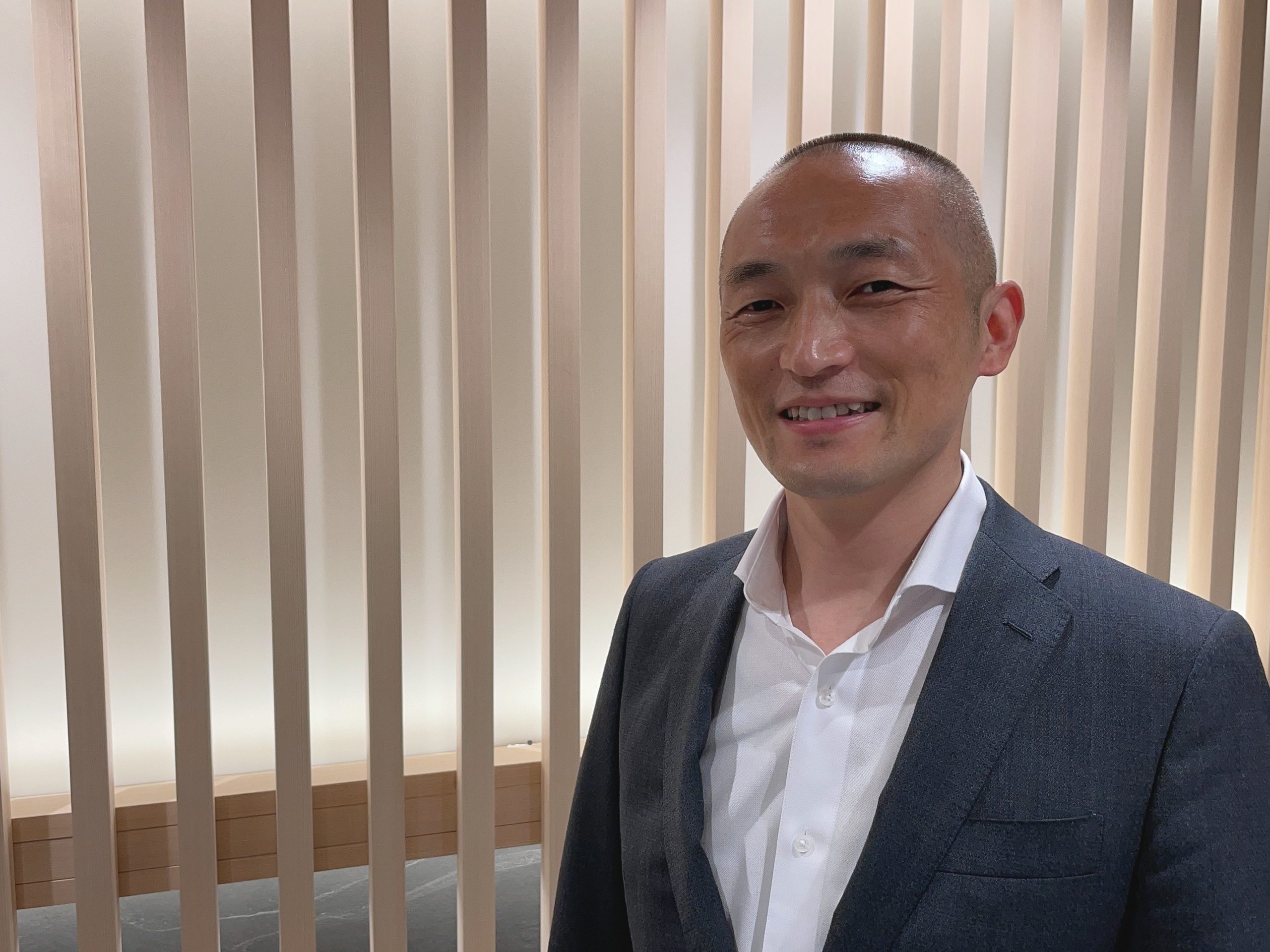
- この記事を監修した人
- 入社後15年間、長野支店にてシステムエンジニアとして活動。
運送業、倉庫業のお客さまを中心に担当し、業務システム構築からインフラ環境構築等の経験を積む。
その後、製造業のお客さまも担当し、rBOM導入のプロジェクトにも関わるように。
16年目に現部門に異動し、rBOM全国支援の担当者となる。
現在はrBOMだけではなく、製造業全般のソリューション提案を手掛けている。
料理が趣味、これからお菓子作りにも挑戦しようか迷っている。 - DAIKO XTECH株式会社
ビジネスクエスト本部
インダストリー推進部 - 田幸 義則
