4M変更とは、製造現場における「人・機械・材料・方法」の変更を管理し、品質の安定と向上を図る手法です。製造業において、高品質な製品を安定的に供給することは、企業の信頼と競争力を維持する上で不可欠です。そのためには、製造プロセスにおけるさまざまな変化を適切に管理する4M変更管理が重要となります。
本記事では、4M変更管理の基礎知識から具体的な手順、課題と対策までを詳しく解説し、製造現場における品質管理の向上に役立つ情報をお届けします。ぜひ本記事の内容を活用して、品質と生産性を向上させてください。
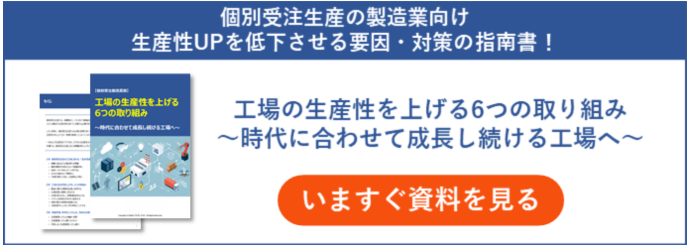
目次
4M変更とは
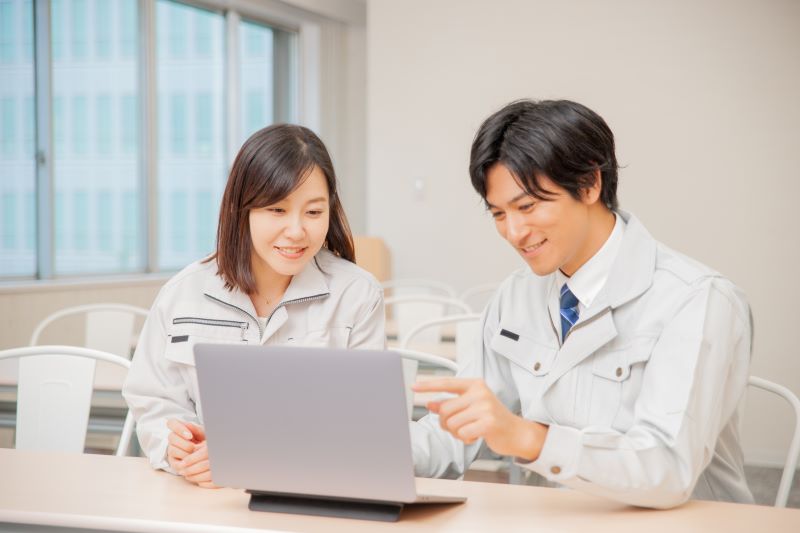
4M変更とは、製造業における品質管理手法の一つです。Man(人)、Machine(機械)、Material(材料)、Method(方法)という4つの要素の変更管理によって、製品品質の維持・向上を目的としています。
製造現場は、常に製品の品質をより良いものにするために動いています。作業員の変更や人員の増加、設備の変更や修理、材料の変更、製造工程や作業方法の変更など、さまざまな変更を行いながら品質の向上を目指します。
これらの変更が適切に管理されていないと、予期せぬ品質トラブルが発生するかもしれません。例えば、新しい作業員が作業に不慣れなためにミスが発生したり、新しい材料が従来の材料と異なる特性を持つために、製品の性能に影響が出たりする可能性があります。
4M変更を適切に管理すると、変更を行う前にその影響を十分に評価し、必要な対策を実行できるため、変更によるリスクを抑えることができます。
そのため、品質トラブルを未然に防ぐことが可能です。
また、4M変更を管理すると、品質トラブル発生時の原因究明を迅速に行えます。変更履歴の記録により、トラブルの原因となった変更を特定し、再発防止策を立てることが可能です。
近年では、消費者のニーズが多様化し、多品種少量生産が主流です。製造現場では4M変更が頻繁に行われるようになり、現場の状況はますます複雑化しています。そのため、4M変更管理は製造業にとってますます重要になってきているといえるでしょう。
4M変更管理は、顧客満足度向上、安全性の向上を図るためにも欠かせません。適切に管理することにより、高品質な製品を安定的に供給し、顧客の信頼を獲得できます。
近年では4Mに加えて、Measurement(測定・検査)とEnvironment(環境)を加えた5M+1E、Management(管理)を加えた6Mといった考え方もあります。
これらの要素も考慮すると、より包括的な品質管理体制を構築可能です。
4M変更の手順
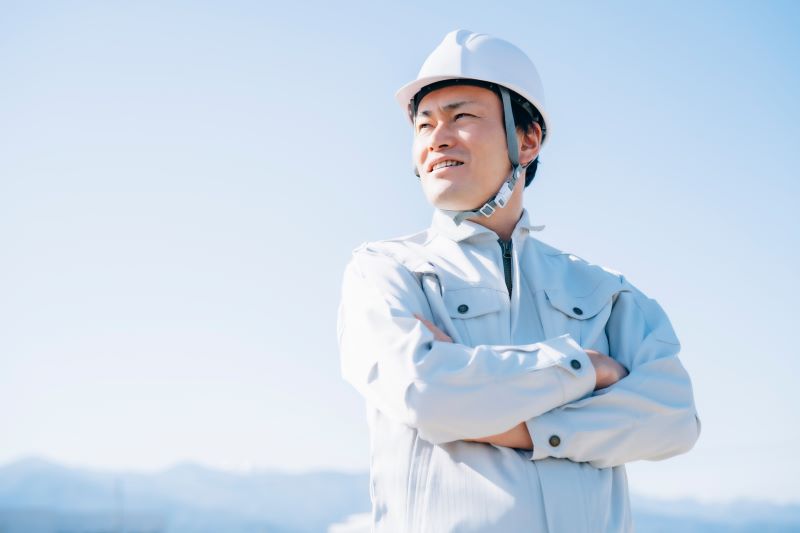
製造現場における品質管理において、4M変更は避けて通れない重要なプロセスです。しかし、闇雲に変更を行うだけでは、期待する効果を得られません。
そのため、効果的な変更を段階的な手順で実施することが重要です。
以下では、4M変更管理を成功に導くための具体的な手順をご紹介します。それぞれのステップを丁寧に確認して、より効果的で安全な変更管理を実現してください。
現状分析と変更点の明確化
4M変更管理の最初のステップは、現状を分析し、変更が必要な点の明確化です。この段階では、現状における問題点や課題の把握が重要です。
具体的には、現在の生産プロセスにおける品質、効率、コスト、安全などの観点から現状を分析します。それぞれの要素において、目標とのギャップや問題点を洗い出します。
例えば以下の分析です。
- 品質に問題がある場合ー不良品の発生率や顧客からのクレームなど
- 効率に問題がある場合ー生産リードタイムや設備稼働率など
- コストに問題がある場合ー材料費や人件費など
- 安全に問題がある場合ー事故発生件数やヒヤリハット事例など
分析結果に基づいて、4Mのどの要素に焦点を当てて改善を行うべきかを検討します。
主には次の通りです。
- 人材のスキル不足が問題であればMan(人)
- 設備の老朽化が問題であればMachine(機械)
- 材料の品質不良が問題であればMaterial(材料)
- 作業方法の非効率性が問題であればMethod(方法)
以上のように、具体的な変更点を明確化します。
変更による影響の予測
変更点が決まったら、次に、その変更によってどのような影響が生じるかを予測します。
この段階では、変更によるメリットだけでなく、デメリットやリスクについての考慮も重要です。
例えば以下のようなケースです。
- 作業員の配置転換を行う場合ー短期的な生産性の低下や作業ミス増加のリスク
- 新しい設備を導入する場合ー初期投資コストや操作習得のための時間
- 材料を変更する場合ー製品の品質や特性への影響
- 作業方法を変更する場合ー作業者の抵抗感や慣れるまでの時間
これらの影響を予測するために、過去の事例やデータ、シミュレーションなどを活用します。また、関係部署や現場の担当者から意見を聞くのも有効です。影響の予測で、事前に対策を検討できます。
変更計画の立案
変更による影響を予測した上で、具体的な変更計画を立案します。
変更計画には以下の内容を明記します。
- 目的
- 内容
- 時期
- 担当者
- 必要な資源
- 評価方法
また、変更に伴うリスクへの対策も盛り込みます。
計画を立案する際には、関係部署との調整や、現場の意見反映が重要です。変更内容を明確に伝えれば、関係者全員が共通認識を持ち、スムーズに変更を進められます。
変更の実施
変更計画に基づいて、変更を実施します。
変更を実施する際には、計画に沿って進めるだけでなく、現場の状況を常に把握し、必要に応じた計画の修正が重要です。また、変更内容を関係者に周知徹底し、協力を得ながら進めることが大切です。
変更実施中は、想定外のトラブルが発生する可能性もあります。そのため、トラブル発生時の対応手順を事前に決めておくのも必要です。
結果の評価と改善
変更を実施した後は、結果を評価し、必要に応じて改善を行います。
評価は、事前に設定した評価方法に基づいて行います。
例えば以下の指標が評価対象です。
- 不良品発生率の推移
- 生産リードタイムの変化
- コスト削減効果
評価結果を分析し、目標達成度や問題点を明確にします。もし問題があれば、その原因を突き止め改善策を検討し、改善策を実施して再度、評価を行います。
4M変更のツールと技法
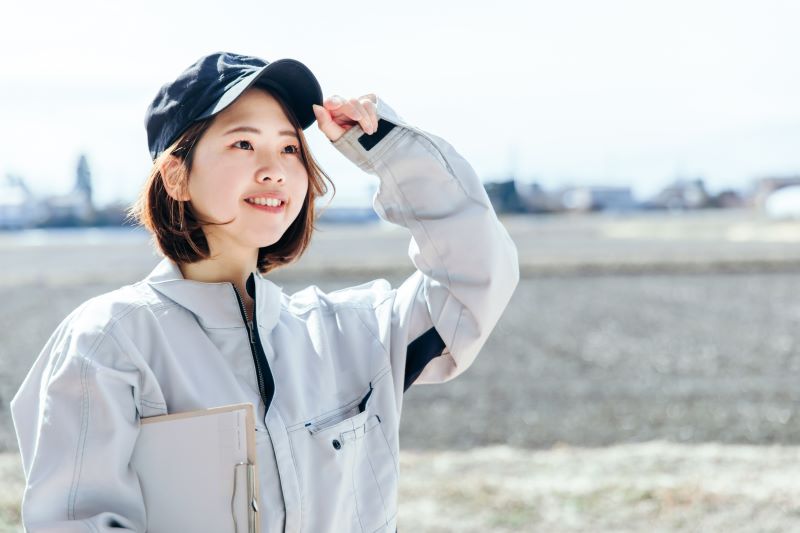
4M変更を効果的に行い、品質向上や効率化を達成するためには、適切なツールと技法の活用が重要です。
状況を的確に把握し、分析し、対策を立てるためのツールや技法を導入すると、よりスムーズで効果的な4M変更管理を実現できます。
4M管理表は、製造現場における品質管理の4M(Man,Machine,Material,Method)の各要素について、現状を把握し、変更点を管理するためのツールです。
4M管理表を用いれば、各要素における現状の問題点や改善点を明確化し、変更内容とその影響、評価方法などを体系的に整理できます。
4M管理表は、以下のような項目で構成されます。
- 項目
- 現状
- 問題点
- 変更点
- 影響
- 対策
- 評価
- 結果
- 考察
4M管理表を活用すると、4M変更を効果的に管理し、品質向上、効率化、コスト削減、安全確保などを実現できます。
QC7つ道具
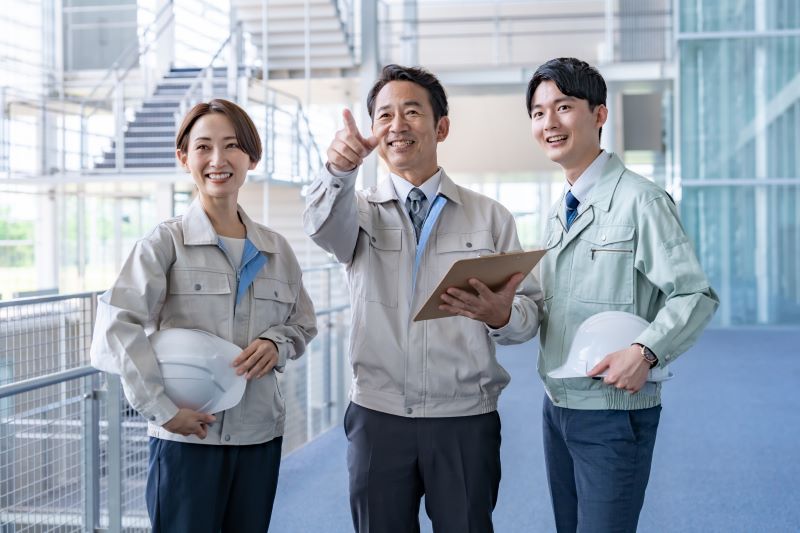
QC7つ道具とは、品質管理において、データを収集し、分析し、問題解決に活用するための7つの手法の総称です。これらの手法を適切に活用すると、品質管理を効率的に行い、品質向上、効率化、コスト削減などを実現できます。
グラフ
データを視覚的に表現すると、傾向や異常値を把握しやすくなります。数値の羅列だけでは見落としがちな情報も、グラフ化により一目で理解が可能です。折れ線グラフ、棒グラフ、円グラフなど、表現したい内容に合わせてさまざまなグラフを使い分けます。
パレート図
パレートの法則とは「80:20の法則」とも呼ばれ、多くの事象において、結果の約8割は、原因の約2割から生じているという経験則です。
パレート図は、このパレートの法則を視覚的に表現するためのグラフです。発生頻度の高い順に問題を並べ、累積構成比を折れ線グラフで示して、どの問題に優先的に取り組むべきかを判断しやすくします。
例えば、製造現場で発生する不良品の原因を分析する場合です。パレート図を作成すると、全体の8割の不良品が、特定の2割の原因(材料の不良や作業ミスなど)から生じていることがわかります。
つまり、パレート図は、限られた資源を効率的に活用するために、重要な少数要因に焦点を当てることを目的としたツールです。
ヒストグラム
データの分布を視覚的に表現することで、ばらつき、中心値、集中度合い、偏り、異常値などを把握できます。製造工程における品質のばらつきを分析する際に用いられるヒストグラムは、その代表的な例です。
散布図
2つの変数の相関関係を分析します。例えば、温度と不良品発生率の関係を調べる際などに活用できます。散布図を見ると、2つの変数間に正の相関、負の相関、または無相関があるかどうかを判断できます。
特性要因図
問題の原因分析で使用する手法です。魚の骨図とも呼ばれ、問題を魚の頭に、原因を魚の骨に見立てて図式化します。複雑な問題の原因を整理し、ボトルネックを特定するのに役立ちます。
管理図
工程の安定状態を監視し、異常を検知します。工程が安定しているかどうかを判断し、異常があれば早期に発見できます。管理図は、製造工程における品質管理に欠かせないツールです。
チェックシート
データを効率的に収集するためのツールです。あらかじめ項目を設けておくことで、データの抜け漏れを防ぎ、正確なデータ収集ができます。チェックシートは、点検作業やアンケート調査など、さまざまな場面で活用されます。
4M変更の課題と対策
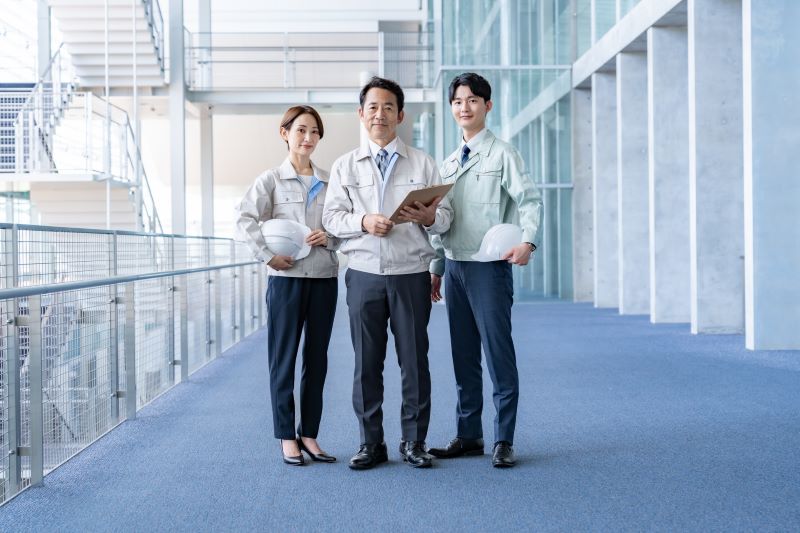
4M変更は、製造現場における品質向上、効率化、コスト削減などを実現するための重要な取り組みですが、同時にさまざまな課題も抱えています。課題を適切に認識し、対策を実行すれば、よりスムーズで効果的な4M変更管理を実現可能です。
以下では、4M変更における代表的な課題とその対策について詳しく解説していきます。
変更の影響を正確に予測することの難しさ
4Mのいずれかの要素を変更する場合、その影響範囲は多岐に渡り、何にどれくらいの影響を与えるのか正確な予測は容易ではありません。例えば、材料を変更すると、製品の品質や特性に影響が出るだけでなく、製造工程や作業者の作業方法にも変更が必要になる可能性があります。
機械を新型に交換する場合、生産効率が向上する一方で、操作方法の習得に時間がかかったり、既存の設備との互換性が課題です。担当者を変更する場合、新しい担当者のスキル不足や経験不足によって、作業ミスや品質不良が発生するリスクもあります。
このように、4M変更の影響は複雑に絡み合っているため、事前にすべての影響を予測するのは困難です。
課題に対しては、過去の事例やデータを分析し、シミュレーションを行い、可能な限り影響の予測が重要です。変更前に関係部署や現場の担当者から意見を聞くのも、予測の精度を高められます。
従業員の抵抗や理解不足
4M変更は、現場の従業員にとって、新たな作業方法や手順を覚え直す必要が生じるなど、負担が大きくなる場合があります。そのため、変更に対して抵抗感を持つ従業員も少なくありません。
変更の目的や内容が十分に理解されないまま変更が実施されると、従業員のモチベーション低下や作業ミスにつながります。
課題を克服するためには、変更の必要性や目的、内容について、従業員に丁寧に説明し、理解と協力を得ることが重要です。
変更によって従業員にどのようなメリットがあるのかを明確に示さなければなりません。例えば、作業効率が向上すると残業時間が減る、新しいスキルを習得できるなどです。従業員にとってのメリットを具体的に示せば、変更に対するモチベーションを高められます。
変更管理プロセスの複雑さ
4M変更は、関係部署との調整や承認、現場への指示、変更内容の記録など、多くのプロセスを伴う複雑な作業です。特に、大規模な製造現場では、変更管理プロセスが煩雑になり、担当者の負担が大きくなる傾向があります。
変更管理プロセスが明確に定義されていない場合、変更内容が適切に伝達されなかったり、変更履歴が記録されなかったりするなど、混乱が生じます。課題を解決するためには、変更管理プロセスを標準化し、明確なルールを設けることが重要です。
変更管理システムなどのITツールを導入して、プロセスの効率化を図ることも有効です。変更管理システムは、変更内容の申請、承認、記録などを一元管理でき、担当者の負担軽減につながります。
4M変更を理解して生産効率を改善しよう
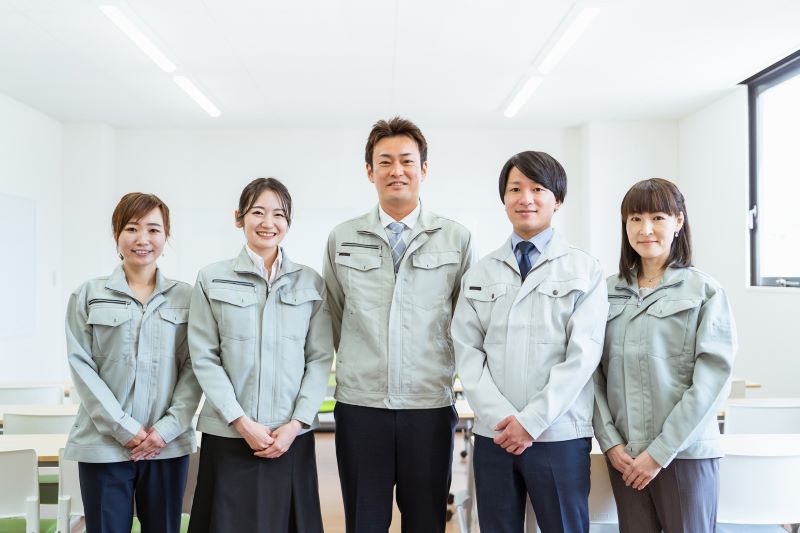
4M変更は、製造業における品質管理と生産管理において不可欠な概念です。Man(人)、Machine(機械)、Material(材料)、Method(方法)の4つの要素を意識して適切に管理してください。品質問題や生産トラブルを未然に防ぎ、生産効率や製品の信頼性を確保できます。
効果的な実施のためには、現状分析、影響予測、計画立案、実施、評価・改善といった手順を踏むことが重要です。4M管理表、QC7つ道具などの技法を活用すれば、より効率的な変更管理が可能です。
4M変更には、予測の難しさ、従業員の抵抗、プロセスの複雑さといった課題が伴います。しかし、過去のデータ分析、従業員への丁寧な説明、変更管理プロセスの標準化といった対策によって克服可能です。
継続的な改善と学習を通じて、4M変更管理のスキルを磨くことが、製造業の競争力強化につながります。
