技術継承の重要性が高まる製造業。中でも個別受注生産の企業は、技術継承が困難と言われています。その要因の一つに「設計の標準化が進まない」ことが挙げられます。
そこで今回、この「標準化」に対しどのように取り組み、技術継承を進めるかをご紹介していきます。
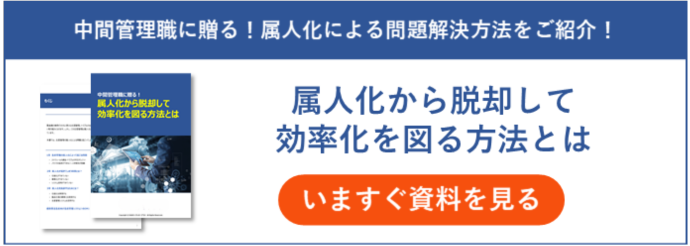
目次
多品種少量生産で育成が困難な理由
製造業における技術の共有・継承をしやすくするためには、まずは標準化を進めることが重要です。これはどの企業も理解しており、幾度となく取り組みを実施していることかと思います。しかし個別受注生産の製造業は、標準化が進まず、技術の共有・継承においてボトルネックとなっているケースが多いようです。
では、なぜ個別受注生産において標準化が進まないのでしょうか。そこには以下のネガティブなイメージが根強くあります。
標準化を進みづらくしているネガティブイメージ
-「顧客に提供するサービス品質をさげてしまう」
個別受注生産において、標準化がネガティブにとらえられる風潮があります。例えば、以下が挙げられます。
- 自社の強みは「1社1社の要求に応えることが強みであるため、標準を押し売るビジネスにしては競争力のある商品を生み出せない」
- とがった企画を立てようと思うと、標準を守っていられない
- 標準は創意工夫を奪う
どれも個別受注生産企業の強みを考慮したもっともな意見です。しかし、このような状況下では、標準化を進めようと標準図などの整備活動を実施しても、実際の案件でそれを使った際、「顧客要求が特殊だから・千差万別だから」という理由で使われないことが多いのです。
「効率化」と「顧客要求への対応」をバランス良く実現する標準をつくらなければ、個別の顧客要求に対応できない“使えない標準”が出来上がってしまうだけです。こうして標準化は一向に進まず、結局設計に依存、属人的な組織となり、技術継承を一層困難にさせ、負の連鎖を続けることとなるのです。
ここまでは個別受注生産における標準化のネガティブな面を整理してきましたが、標準化は企業側に「技術の共有・継承の簡略化」をもたらします。そこで次に標準化を進める上で個別受注生産の人材育成において、どのようなメリットをもたらすのかをご紹介していきます。
標準化がもたらす技術継承・育成へのメリット
「効率化」と「技術の高度化」の必要性
「効率化」とは、自社で蓄積されたナレッジ(他の案件での工夫や苦労)を多くの社員に共有することで、同じように悩み、同じ失敗を繰り返して手戻りが起きるのを防ぎます。また、過去の類似案件が共有されていることで、ゼロから設計をする必要がない案件も増えていき、作業の効率化を図ることができます。
一方で「技術の高度化」は、効率化して時間が生まれたら高度化できるのかといえばそうではありません。企業のナレッジを蓄積し、設計を高度化させる必要があります。
技術を高度化させ競争力のある製品を生み出すためには、何が新しいと知るのか、何をもって新しいと認識するか、がポイントとなります。過去を知っているから何が新しいかを知ることができ、常識を知っているから個性を認識できます。これをふまえれば型にはまらないカスタマイズ設計をするには、「過去に行った設計内容を知らずして、新しいモノの設計開発・技術の向上は困難」といえるでしょう。そのためにも、過去の設計の工夫を積み重ねた「標準」を明確にしておく必要があるのです。
効率化し、過去を理解し、新しいことを考えて、高度化していく。このように「標準」を土台とし、技術継承、進化を進めていくことが必要です。そこで企業は、自社の蓄積した技術を継承させるために、標準という土台づくりが重要なのです。こちらを踏まえたうえで、標準化がもたらすメリットをみていきましょう。
ナレッジ情報の共有と時間短縮をさせるには
設計の標準化を実施し、ナレッジ情報の検索時間を大幅に短縮するためには設計データの一元化を行います。これは、データが自分のパソコンの中(ローカル)にだけ残った状態になり、他の人が見られない状態から脱却するということです。データを入れる仕組みを作っても、実行をしなければ意味がありません。そのデータをきちんと検索できるよう部門内、部門間(営業、資材、製造、経理・経営)を横断したデータ共有をする必要があります。
このように一連の業務をシステム化することにより、関連資料の一元化が容易にできます。保管している過去の情報をすばやく調べられるので、類似の図面を探す時間を短縮して、容易に流用できるようになります。そのため、ベテラン設計者の部門表や図面を参照しやすくなり、ノウハウの継承がやりやすくなるでしょう。このように必要な情報を必要なときに取り出せることで、個別受注生産において設計の標準化の実現を目指せます。
特に個別受注生産企業の設計部門は多忙を極めているのが現状です。設計標準がなく仕事をしていると、毎回図面を書かなければならなくて非効率です。さらに、他の案件での工夫や苦労が共有されていないので、同じように悩み、同じ失敗を繰り返して手戻りが起きます。
そのような中で設計を標準化できれば、個別に仕様を検討せずに過去の図面を流用でき、また部品を共通化できればロット切り替えの時間に悩まずに済み、教育する手間、時間の削減をすることが可能です。
標準化に欠かせない個別受注生産専用の生産管理システム
では標準化が難しい個別受注生産において、どのように標準化を進めナレッジの共有、蓄積をし、教育の手間を省くことができるのでしょうか。それは「個別受注生産専用の生産管理システム」を導入することがポイントとなります。
過去案件情報の一元化を実現する「rBOM」
そこでDAIKO XTECHでは、個別受注生産企業の標準化に特化した製品「rBOM」をご提供しております。
このrBOMに、設計者の経験値や改善データを蓄積させ、設計情報の非属人化による品質を安定させ、さらに過去の情報を抽出し高度化を図ることができ、設計の標準化・育成の簡略化を支援しております。ご興味のある方、またrBOMについて詳細を知りたい方は、ぜひ下記より資料をダウンロードいただき、貴社の設計の標準化推進にお役立てください。
BOMの統合により情報共有をシームレス化。
リアルタイムな進捗・原価把握を実現する生産管理システム「rBOM」については、下記よりご覧いただけます。
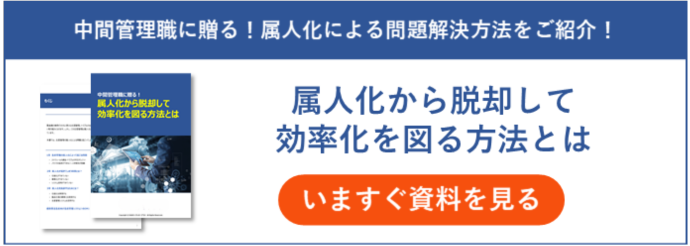
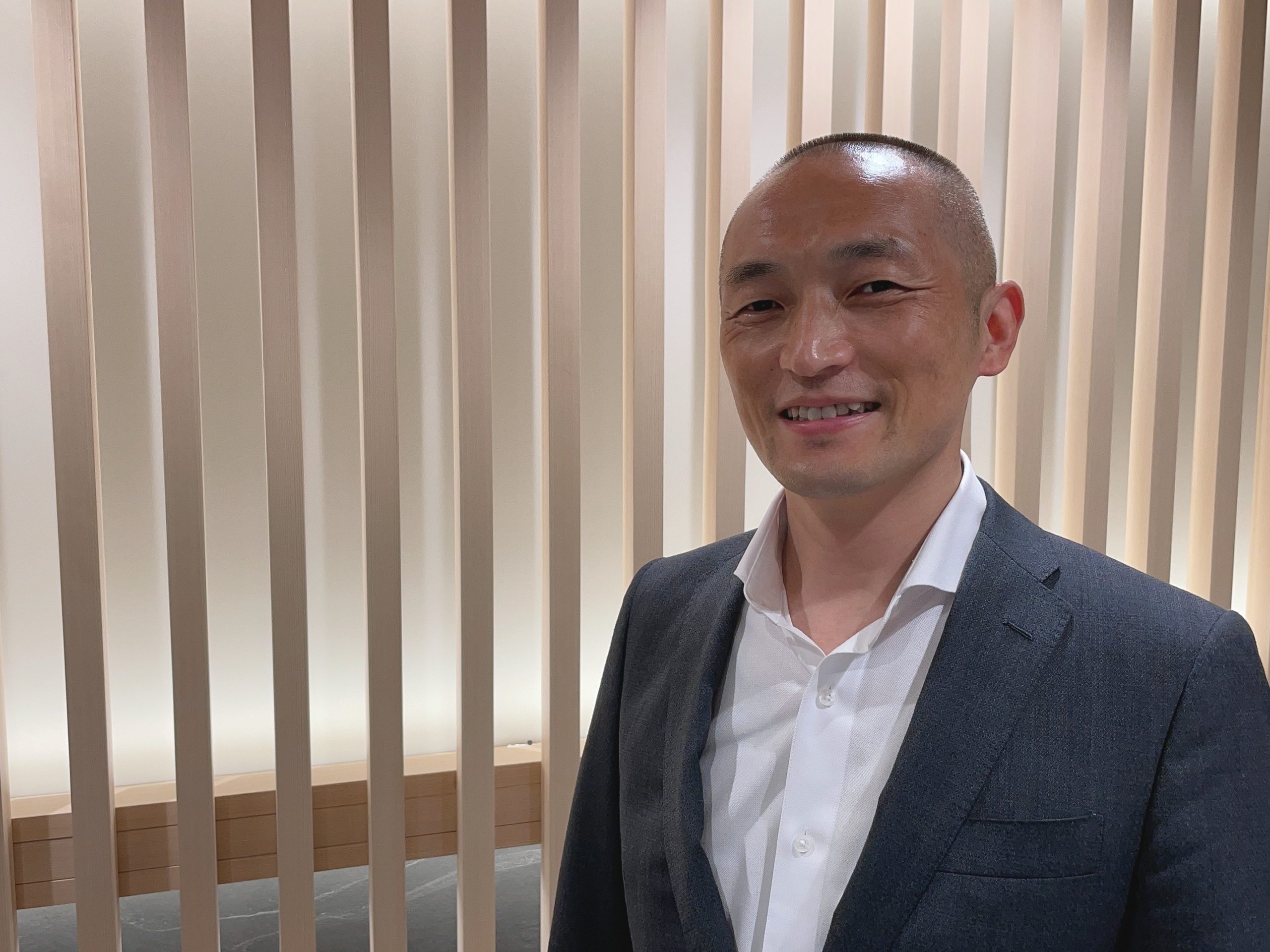
- この記事を監修した人
- 入社後15年間、長野支店にてシステムエンジニアとして活動。
運送業、倉庫業のお客さまを中心に担当し、業務システム構築からインフラ環境構築等の経験を積む。
その後、製造業のお客さまも担当し、rBOM導入のプロジェクトにも関わるように。
16年目に現部門に異動し、rBOM全国支援の担当者となる。
現在はrBOMだけではなく、製造業全般のソリューション提案を手掛けている。
料理が趣味、これからお菓子作りにも挑戦しようか迷っている。 - DAIKO XTECH株式会社
ビジネスクエスト本部
インダストリー推進部 - 田幸 義則
