モノづくり企業の中にはさまざまな部門がありますが、特に生産管理部門は業務が幅広く、業種によって仕事内容は異なります。
本記事では生産管理の基本的な仕事内容をご紹介しながら、生産方式別の生産管理の特徴や実際のDX事例について解説します。
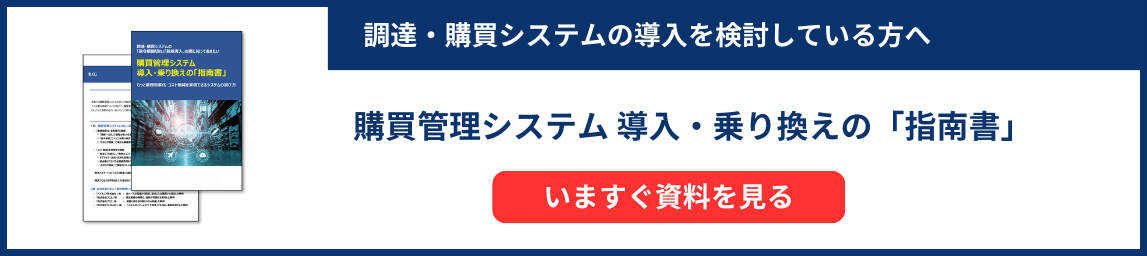
目次
工場内での生産管理の目的と位置付けとは
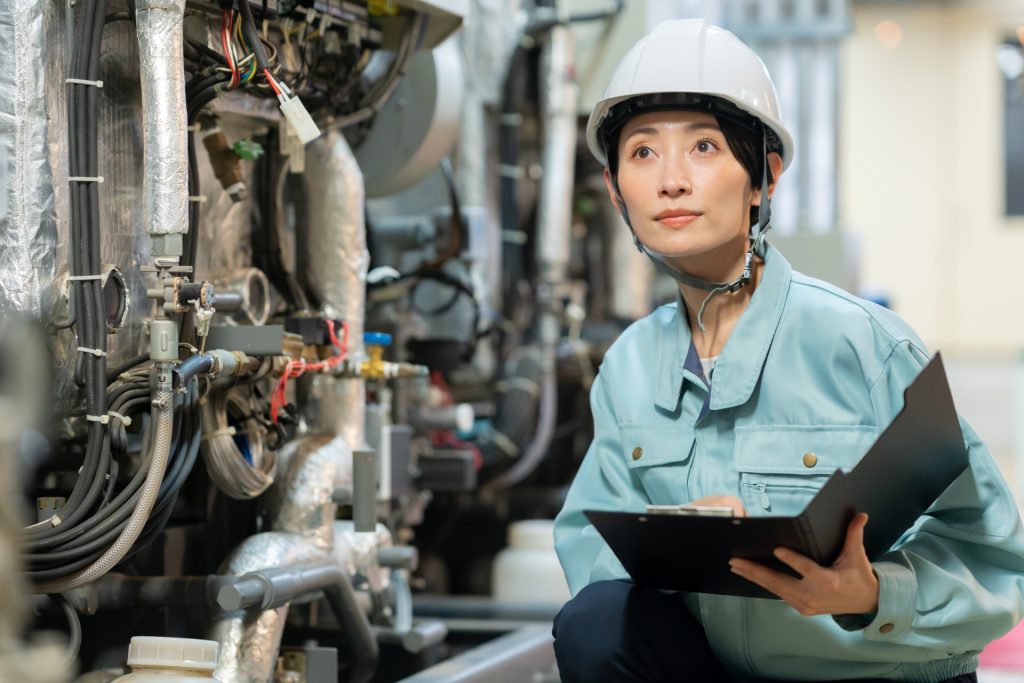
モノづくりを行う工場内には複数の部署が存在します。その中でも生産管理部署は、工場全体の製造プロセスを統括する重要な役割を担っています。
生産管理部署の主な業務は以下の通りです。
- 需要の予測
- 資材の調達
- 製造現場の管理
- 納品予定日の設定と管理
- 顧客への納品までの全工程の把握と管理
これらの業務を通じて、生産管理部署は製造工程全体を効率的に運営し、スムーズな製品供給を実現しています。
本章では生産管理の目的や、工場内での他部署との関連性・位置付けについて解説します。
生産管理の目的
工場に生産管理の部門を置く目的は、QCDのバランスを取りながら維持し、向上させることです。
QCDとは、製造に欠かせない3要素です。
- Q:Quality(品質)
- C:Cost(コスト)
- D:Delivery(納期)
以上の3要素から成り立っています。
もっとも重要なのは品質ですが、コストや納期を無視すると顧客の要望を満たせません。
コストを軽視すると利益が出なくなり、納期を軽視すると顧客の信用を失う可能性があります。
生産管理の部門では、QCDのバランスを取りながら維持・向上させる必要があります。
具体的には、以下のような方法でQCDの維持・向上に取り組みます。
- 品質の向上:作業工程を改善し、製品の品質向上を目指す
- コスト管理:原材料費や人件費など、製造に関わるコストを考慮して、資材の発注や工期を把握し、コストに見合った調整を行う
- 納期管理:顧客と取り決めた納期を守るように管理し、特殊な事情がある場合には顧客への納期交渉も行う
QCDについて、詳細は下記記事をご参照ください。
工場内での生産管理の位置付け
次に、工場内において、生産管理は幅広い工程に関わり調整を行うため、工場長の役割とも言えます。
受注生産を行うモノづくり企業の仕事の流れを見ながら、生産管理の位置付けについて解説します。
受注生産を行う場合、工場内の業務の流れは一般的に以下の通りです。
- 受注管理
- 設計・開発
- 生産計画
- 調達
- 生産
- 検査
- 納品
受注管理
受注管理の内容は、具体的には以下の通りです。
- 営業部門が顧客と契約を結ぶ
- 見積の取り交わしをする
- 受注製品の注文管理や顧客とのやり取りを行う
設計・開発
設計・開発の業務内容は具体的には以下の通りです。
- 顧客の要望を元に製品の設計や開発を行う
- 製造部門と連携して試作品を作り上げる
生産計画
設計・開発部門や顧客の要望に基づき、納期に間に合う生産計画を策定します。
生産
生産計画に遅延が発生しないよう、進捗状況を確認しながら製品を生産します。
検査
出荷前に製品の品質を検査し、製品の梱包などの出荷準備を行います。
納品
製品が出荷されてから顧客に届くまでを管理します。
上記の流れで受注生産を行いますが、生産管理に関わる部分を図解すると以下の通りです。
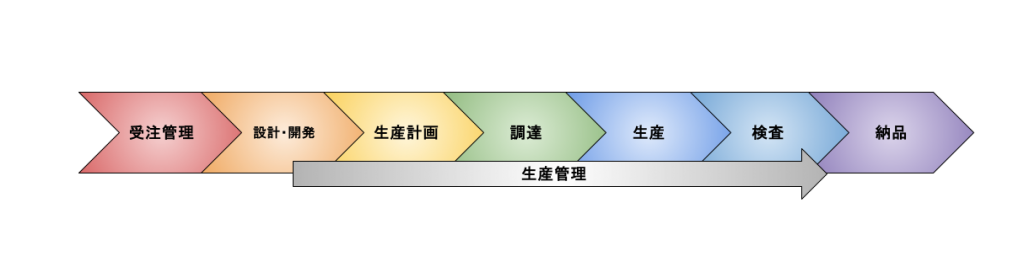
生産管理は、上記のように受注後のすべての流れについて関連します。
よって、ある意味では工場長のような役割を果たすとも言われます。
生産管理の工場での仕事内容とは
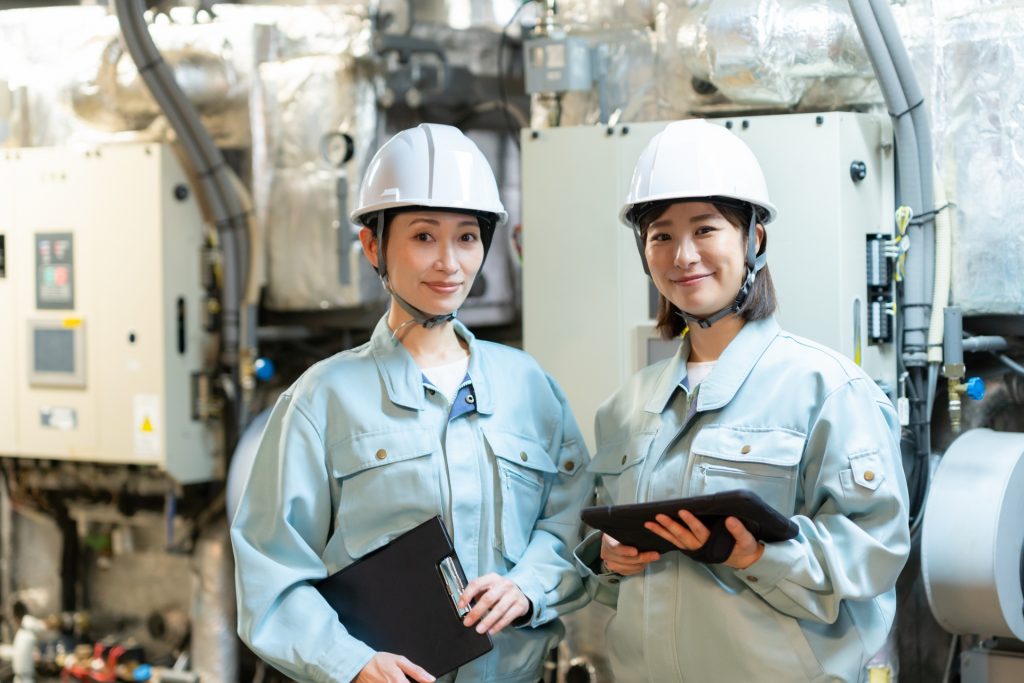
次に、生産管理の工場での仕事内容を具体的にご紹介します。
生産管理の仕事内容は主に以下の6種類です。
企業によっては、品質管理部門が独立していたり、調達購買を専門部署が担当したりする場合があります。ここでは、一般的な生産管理の仕事内容をご紹介します。
- 需要予測
- 生産計画
- 調達購買
- 工程管理
- 品質管理
- 原価管理
以下で詳しくご説明します。
需要予測
効率的な生産を行い、在庫のムダをなくすためにも、需要予測は重要な業務です。
自社での販売実績や市場でのトレンド、競合となる企業の動向、経済指標といった要因を考慮し、需要予測をしなければなりません。
また、需要予測の精度向上にも取り組んでいます。
まずは、下記の手段を用いて需要の予測を行います。
- 過去のデータや顧客の購買動向、他社動向から予測
- 経済指標やビッグデータを活用した予測
- AIによる予測
市場データと統計データを活用し、より正確な予測を行えるようにします。
しかし、需要予測をして終了するのではなく、予測精度の検証が重要です。
定期的に予測と実態の誤差を検証し、要因分析を行います。
また、需要予測は生産量を最適化するためだけでなく、設備投資の必要性を測り、人員配置計画のためにも重要です。
需要予測の具体的な手法について以下の記事で解説しているため、ぜひご一読ください。
需要予測の重要性を徹底解説|5つの手法と精度向上のためのポイント
生産計画
需要予測に基づいて生産計画を立てます。
生産計画とは、生産量や時期についての計画であり、具体的には以下の事柄について計画を立てます。
- 製品の種類、製造方法、数量、納期
- 原材料や部品の調達方法や必要数量
- 製造から納期までの具体的なスケジュール
上記の内容を含めた生産計画を元に、人員配置や必要コストの計算が行われます。
生産計画における日程計画の種類
生産計画は大きく、大日程計画・中日程計画・小日程計画に分けて計画されます。
以下で詳しく解説します。
①大日程計画
大日程計画は、3カ月から12カ月の長期にわたる計画のことで、需要予測を元に全体の方向性を決めます。
大日程計画では、具体的に以下のような計画を立てるのが一般的です。
- 予定生産量を達成するための設備投資計画
- 長期的な人員計画の策定
- 新製品開発や既存製品の改良計画
状況に応じて適宜見直しを行います。
②中日程計画
中日程計画は、1カ月から3カ月程度の中期計画のことで、より実務的な計画を立てていきます。
中日程計画では、具体的に以下のような計画を立てるのが一般的です。
- 生産能力計画
- シフトなどの中期的な人員計画
- 月ごとの生産計画
- 原材料、部品等の調達計画
具体的な計画のため、状況の変化だけでなく、数週間〜1カ月程度のペースで見直しを行うと良いです。
③小日程計画
小日程計画は、1週間〜1カ月程度の短期計画のことで、毎日の生産状況進捗を管理するための計画です。
実際の作業に関する計画であるため、専門性が高く複雑な設計が必要です。
よって、計画を立てる人員には高度な知識と経験が求められます。
小日程計画では、具体的には以下のような計画を立てるのが一般的です。
- 各工程の具体的な作業スケジュール
- 機械の稼働計画
- 検査日程や手順
小日程計画は具体的な作業スケジュールでもあるため進捗を常に確認し、毎日〜1週間程度での見直しを行いましょう。
ご紹介した生産管理に関する日程計画は、立案するだけでなく定期的な進捗確認や見直しが重要です。
納期遅れや品質悪化につながらないためにも、計画段階でできる限り無理のない計画を立てることを意識しましょう。
さらに詳しい生産計画の立て方やポイントについては、以下の記事をご参照ください。
生産計画とは?ムリ・ムダのない計画の立て方やポイントをご紹介
生産計画の種類
生産計画には、プッシュ型とプル型の2種類の方法があります。
①プッシュ型
プッシュ型は、押し出し方式とも言われる生産計画の一種です。
まず、工程をより原材料に近い「上流工程」とより製品に近い「下流工程」に分けます。
上流工程で原材料から半製品や中間品を製造し、下流工程へ加工や生産の指示を行います。
生産計画通りに作業を進めやすいことが特徴的であるものの、変化に弱く、次々に作っていくため作りすぎのムダが出やすいことには注意が必要です。
医薬品、化粧品、食品工場などはプッシュ型で生産を行っているケースが多いです。
万が一事故や不良品が出てしまった場合に、工程ごとに作業の確認ができることも利点です。
②プル型
プル型は、引っ張り方式とも呼ばれる生産計画の一つです。
プッシュ型とは対照的に、下流工程から上流工程へ、原材料等の供給を指示して、下流工程で組み立てや生産を行います。
製品の生産ペースや必要量を需要に合わせて調整できるため、作りすぎのムダが出づらいことが特徴です。
効率的な生産ができる一方で、原材料や部品のストックについてどれくらいの種類や量を保管しておくべきかといった点では、緻密な需要予測や保管体制が重要です。
また、急な増産体制には対応しきれない点に注意が必要です。
トヨタ生産方式に代表される「かんばん方式」はプル型の代表例です。
かんばん方式とは、必要なものを必要なときに、必要な量生産するジャストインタイム(JIT)を達成するための生産管理方式です。
かんばんは前工程への発注書のようなもので、品名や品番、数量や運搬情報などの情報が記載されています。
具体的には以下のような手順で運用します。
- 後工程から前工程へかんばんを渡す
- 前工程はかんばんに書かれた数量を生産
- 前工程から後工程へ製品とかんばんを渡す
- 後工程が製品を加工する
- 製品の加工が終わったらかんばんを取り外し、また前工程へ渡す
- 2.からの工程を繰り返す
自動車メーカーなど、サプライヤーとの関係が強固な企業では、原材料や部品の調達が円滑に進むことが多いです。しかし、中小企業では原材料や部品の在庫管理が難しくなるというデメリットも理解しておく必要があります。
調達購買
調達購買とは、製品に必要な原材料や部品、資材などについて仕入先を検討し、価格交渉、自社内の調整や検収を行う業務です。
生産計画を元に、以下の点に留意しながら仕入先を決定します。
- 利益が出るような価格で仕入れる
- 生産に遅れが出ないように納品する
- 品質の良い原材料や部品を仕入れる
調達購買においても、QCDの最適化を重視してサプライヤーを選定しましょう。
安易に低価格を求め、サプライヤーに無理な見積もりを要求すると、取引を拒否されたり、品質の悪い部品による事故につながる可能性があります。
自社と仕入先双方が納得できる価格交渉を行う交渉技術も重要です。
調達購買の詳細については、以下の記事をご参照ください。
工程管理
工程管理とは、製造が始まったところから進捗状況を把握し、効率的に製造できるように管理を行うことを指します。
工程管理の段階では、特に品質の維持と納期順守に重点を置き、全体を見渡さなければなりません。
- 関係各所とコミュニケーションを取り、情報収集して判断する
- 納期遵守のために全体を調整する
- トラブルに対して臨機応変に対応する
上記のような対応力が重要な仕事です。
山積みと山崩しとは
工程管理において、負荷配分は重要な要素です。
負荷配分とは、原材料や部品、人員配置、労働時間といった生産のために必要な限られた要素を適切に配分する作業を言います。
具体的には、山積みと山崩しの2種類の考え方があります。
①山積み
山積みは、工程内の一定の時期の負荷を積み重ねる方法です。
一旦生産能力などの要素を度外視し、単純に納期を考え作業工程を積み上げていきます。
上記の方法でできあがる工程表を「山積み工程表」と言います。
時間を縦軸に、人員や設備などの資源を横軸にして棒グラフで表すのが一般的です。
簡単な図で表すと、下図のような棒グラフが一つの例です。
棒グラフの青い部分は負荷に余裕がある状態で、赤線より上の部分は負荷が超過してしまっている部分を表します。
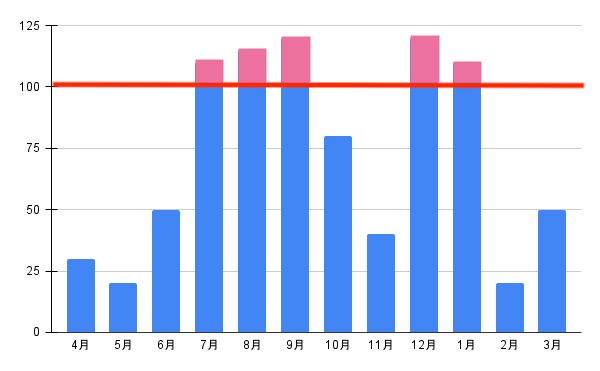
②山崩し
山崩しとは、山積み工程表から個人の作業能力や実際の作業量を元に能力線を引き、能力線からはみ出た作業を平準化する方法です。
期間ごとの作業量や進捗状況を把握しながら、はみ出てしまった負荷の振り分けを行います。
フォワード方式とバックフォワード方式
負荷配分についてはさらに、フォワード方式とバックフォワード方式に分かれます。
①フォワード方式
フォワード方式とは、順行負荷法とも呼ばれる負荷配分方式を指します。
日程計画を起点として、時系列順に負荷を積み上げていく方法です。
工程での作業開始から完了までを順番に記載し、最終的な納期がいつになるのか計算をします。
受注前に納期を予測したり、顧客と最終納期を調整して決定する前に活用したりするのが一般的です。
②バックフォワード方式
バックフォワード方式は、逆行負荷法とも呼ばれる負荷配分方式です。
納期を起点とし、作業完了日から作業開始日に向かって、時系列とは逆に負荷を積み上げていく方式です。
顧客と納期を確定させた後に活用するのが一般的です。
時間軸とは逆方向に負荷を計算しなければならず、先の日程の予測や調整が必要となった場合には複雑な計算や見直しが必要です。
なお、工程表を完成させるには以下の方法があります。
- 手書きの棒グラフ
- Excel等の表計算ソフト
- 工程管理に関するシステム活用
手書きやExcelで作成する工程表は、自由度が高い反面、工程管理が属人化しやすく、ミスが発生しやすいというリスクがあります。また、経験や勘に頼った計画になりがちです。
工程管理にもシステムを取り入れると、属人化や計算ミスによる事故を防ぐことも可能です。
工程管理については、以下の記事でも詳しく説明しているため、ぜひご一読ください。
工程管理とは?製造業における基本手順や効率化する方法をご紹介
品質管理
品質管理は、生産工程の中で一定の品質を保てるように管理する業務です。
QCDの中でも品質は最優先事項であるため、品質管理のみで独立した大きな部門としているモノづくり企業も多く存在します。
品質検証や品質改善が主な業務です。
①品質検証
品質検証では、完成品の品質だけでなく、原材料や部品が十分な品質基準を満たしているか検査します。
また、工程が品質を保てる能力を有しているかの検証や、適切な管理がなされているかについても検証を行います。
②品質改善
品質改善では、大きく「再発防止」と「未然防止」の観点で改善を行います。
再発防止とは、既に発生した事故などに対して、現状を把握し、原因を分析して再発防止策を講じることです。
一方で、未然防止とは、トラブル事例などから現在の生産方法や工程で将来起こりうるリスクを想定して、将来類似のトラブルや事故を未然に防ぐことです。
以下で品質管理と品質保証の違いや、品質に関する規格や手法を解説します。
品質管理と品質保証の違い
品質管理と混同しやすい用語として、品質保証が挙げられます。
品質管理とは、資材の調達から製造、出荷に至るまで、工場全体の品質を維持する取り組みを指します。
一方で、品質保証は完成品が顧客満足を満たしているか見直し、社内へフィードバックを行うことを指します。
品質管理は製造過程における製品の品質維持を目的とし、品質保証は完成品の品質向上を目的とするという点で大きく異なります。
ISO9001とは
品質に関する規格の一つに、ISO9001が挙げられます。
ISO9001とは、品質マネジメントシステムに関する国際規格です。
ISOとはスイスのジュネーブに本拠地を置く国際標準化機構という非政府機関で、製品やサービスについて世界中で同じ品質・レベルのものを提供できるように国際規格を制定しています。
ISO9001は、一貫した製品・サービスの提供と顧客満足の向上を実現するために多くの要求事項が定められています。
品質の良い製品を作るだけでなく、プロセスを継続的に改善していく仕組みを作ることも要求されます。
厳しい要求事項がある一方で、ISO9001の認証を取得すると以下のような効果があります。
- 業務効率の改善や組織体制の強化
- 法令順守の推進
- 仕事の見える化による業務継承の円滑化
- KPIの管理
- リスクマネジメント
- 継続的な改善による企業価値の向上
- 海外企業を含む取引要件の達成
- 品質保証による社会的信頼や顧客満足の向上
引用:概要 | ISO 9001(品質) | ISO認証 | 日本品質保証機構(JQA)
高品質な製品やサービスを継続的に提供できる企業であることの証明となり、受注活動で有利になることがあります。また、社内では継続的に品質に対する意識を維持できるという利点もあります。
QC7つ道具とは
品質管理は、英語のQuality Controlを略して「QC」とも呼ばれます。
品質管理を行う手法として、QC7つ道具の活用も挙げられます。
- グラフ
- チェックシート
- パレート図
- ヒストグラム
- 特性要因図
- 散布図
- 管理図
以上の7つの手法を合わせて「QC7つ道具」と言います。
一つずつ解説します。
①グラフ
データを視覚化するために、品質管理ではグラフの活用は欠かせません。
適切なグラフを選択しないと、良質なデータが得られても正確な評価ができません。
モノづくりではあらゆるデータ分析を行うため、グラフの使い方についてはしっかりと教育を行いましょう。
例を挙げると、以下のように目的に合わせてグラフを利用します。
- 変動を見たい場合:折れ線グラフ
- 数量を比較したい場合:棒グラフ
- 比率を見たい場合:円グラフ
- 比率を比較したい場合:帯グラフ
- バランスを見たい場合:レーダーチャート
②チェックシート
チェックシートは、点検や記録を行うために活用します。
品質低下を防ぐために、予め必要なチェック項目を定めておき、日常点検や定期的な検査に活用します。
チェックシートは形骸化してしまうことも多々あるため、定期的に見直しを行い内容をアップデートする必要があります。
③パレート図
パレート図は、品質管理では不良品の原因と優先して対応すべき対策を決めて問題解決を図る際に有効です。
項目別のデータを値の大きな順から棒グラフで並べ、累積比率を折れ線グラフで表します。
下図のように、一番左に位置する項目がもっとも比率が多く、優先して対応すべきであると判断できます。
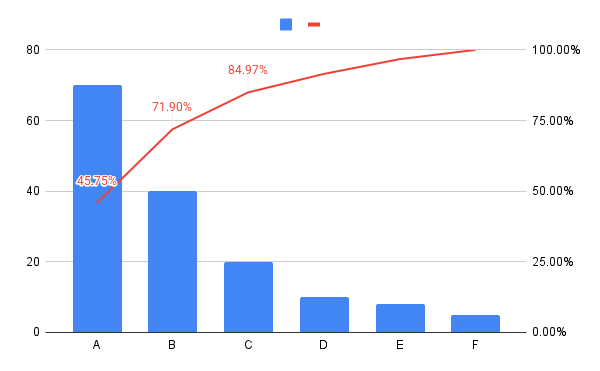
④ヒストグラム
ヒストグラムは度数分布図とも呼ばれ、データを定めた区間ごとに区切り、棒グラフで各区間の数値を表します。
データのばらつきを確認するために活用します。
品質管理では、製品の精度や不良品の割合を把握し、不良の原因を確定するためにヒストグラムを活用します。
グラフの山が規定値でもっとも高く、幅が狭いグラフになるような品質管理が理想的です。
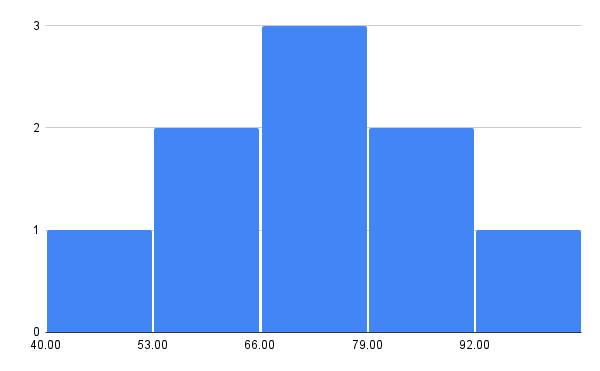
⑤特性要因図
特性要因図は、問題が起きた際や課題を発見した際に、要因をあぶり出すために用いられます。
完成した際には魚の骨のように見えるため、フィッシュボーン図と呼ばれることもあります。
下記の手順で要因分析を進めていきます。
- 魚の頭部分に課題や問題を書く
- 魚の背骨を書き、枝分かれするように大骨に思いつく大きな要因を書き出す
- 大骨からさらに枝分かれして、小骨を書くように大きな要因を引き起こす要因を細かく挙げていく
- 3.の大きな要因から小さな要因を書く作業を繰り返すことで、細かな要因を洗い出す
大骨部分に4M(Man:人、Material:材料、Machine:機械、Method:方法)の視点を取り入れると、より客観的な要因分析が可能です。
⑥散布図
散布図は、2つのデータの関連性を調べるために利用します。
2種類のデータを縦軸と横軸に置き、点を打って(プロット)いきます。
製造現場では、製造条件と不良率・厚さと耐久性など2つの関連性を調べるのに用いられます。
- 点の集合が右上がりの直線上:相関関係が強い
- 満遍なく点が散らばる:相関関係が薄い
一般的には以上のように判断できます。
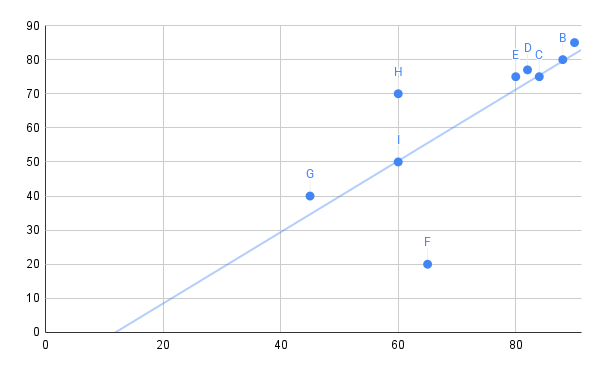
⑦管理図
管理図とは、製品のばらつきが規定値内におさまっているかどうかの判断に活用されます。
下記の3つの線から成り立ちます。
- 上方管理限界線(UCL)
- 中心線(平均値)
- 下方管理限界線(LCL)
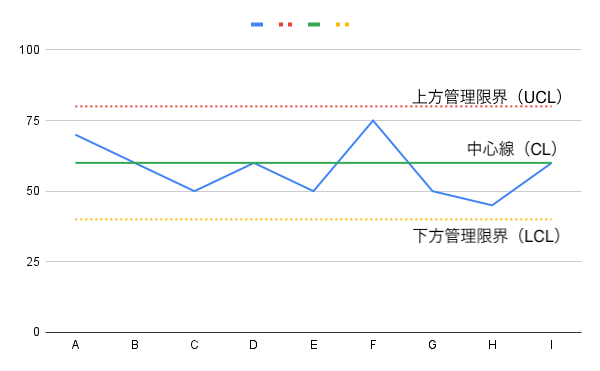
中心線と折れ線グラフが近い値を示していれば、品質が安定していると判断できます。
上図のようにばらつきがある場合は、中心線を上下した折れ線グラフを描きます。
管理限界内であれば許容範囲内と判断できますが、将来的な問題発生を防ぐために、できる限りデータを中心線に近づける改善活動が必要です。
原価管理
原価管理は、商品やサービスの生産コストを最適化するための取り組みを行うことです。
生産にかかわる全体的なコストを軽減して、利益を最大化するために戦略的に取り組みを行います。
一般的には以下の手順で業務を進めていきます。
- 標準原価の設定
- 原価計算
- 原価差異分析
以下の記事で標準原価や原価計算について詳しくご紹介しているため、ぜひご一読ください。
原価計算とは?標準原価・見積原価・実際原価の計算方法【具体例】
製造業における生産管理の課題とは
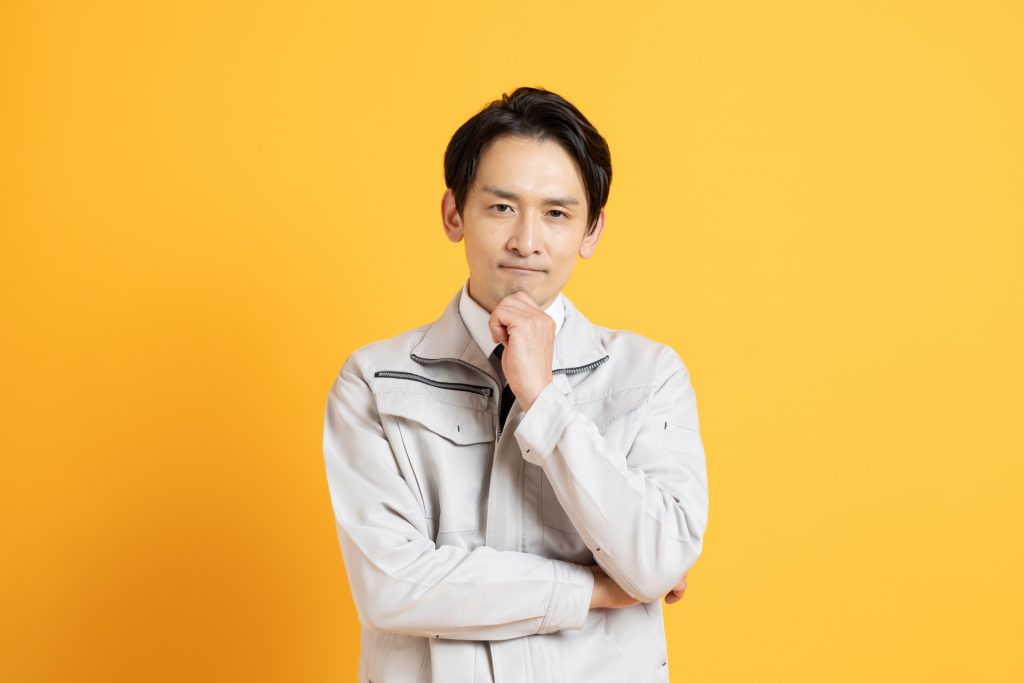
製造業における生産管理の課題には、主に以下のような点が挙げられます。
- 工程の進捗管理が難しい
- 負荷配分を行うにあたって負荷計算ができない
- 経験や勘に頼った計画や予測が多い
- 部門ごとにITツールを活用しており横断性がない
- 不良やトラブルの発覚が遅れてしまう
以下の記事にて、生産管理の課題を解説しているため、ぜひご一読ください。
製造業における生産管理とは?目的・役割からよくある問題・課題まで解説
生産方式別に見る生産管理の特徴
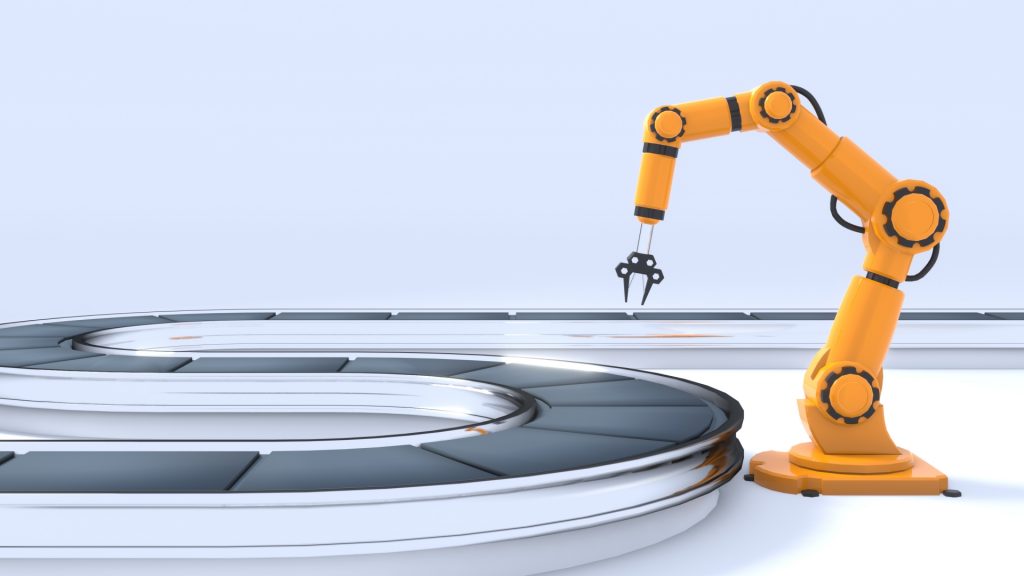
製造業には顧客の要望や商材、ターゲットによってさまざまな生産方式があります。
本章では、生産方式別に生産管理の特徴をご紹介します。
大量見込生産型工場の場合
大量見込生産型の工場は、市場の需要に合わせて標準化された製品を大量生産するのに適しており、自動車部品や家電製品などの製造に用いられます。
大量見込生産型工場の生産管理のポイントは以下の通りです。
- 各工程の作業時間の平準化
- 製品切り替えのダウンタイムを最小限にする
- 品質のばらつきを抑えて安定した品質水準を保つ
- 需要変動に対応できるように設備対応や多能工化を進める
個別受注生産型工場の場合
個別受注生産型工場は、顧客の要望に応じて設計から製造まで行います。
顧客の仕様に基づいた設計が必要な産業機械や特注設備などの製造に適しています。
個別受注生産型工場の生産管理のポイントは以下の通りです。
- 受注〜設計〜製造のリードタイム短縮
- 設計変更へ柔軟に対応する
- 受注ごとのコストや納期管理を厳密に行う
- 原材料や部品の調達管理でも汎用部品を用いるなど工夫する
ロット生産型工場の場合
ロット生産型工場は、同じ種類の製品をロット単位でまとめて生産します。
電子部品や金属加工部品など、同じ製品を一定数まとめて製造する製品に向いています。
ロット生産型工場の生産管理のポイントは以下の通りです。
- 設備の稼働率を最大化し、複数の生産スケジュールを管理する
- 各工程の作業内容や時間を正確に把握して、柔軟な生産計画を行う
- 作業を標準化したり、工具を共通化し段取り切り替えを短縮する
- 品質管理では製品ごとに記録を残し、トラブル時に追跡できるよう備える
バッチ生産型工場の場合
バッチ生産型工場では、原材料を一定量ずつまとめて処理して製品を生産します。
化学製品や食品などプロセス型の生産方式に向いています。
バッチ生産型工場の生産管理のポイントは以下の通りです。
- 温度、圧力、流量、混合比率など製造パラメータのリアルタイム監視と制御
- 工程内品質保証を徹底し、中間品の品質チェックも厳格に行う
- 化学製品においては特に環境規制・安全基準の遵守
生産管理でAIを活用し工場内のDXを進めた事例
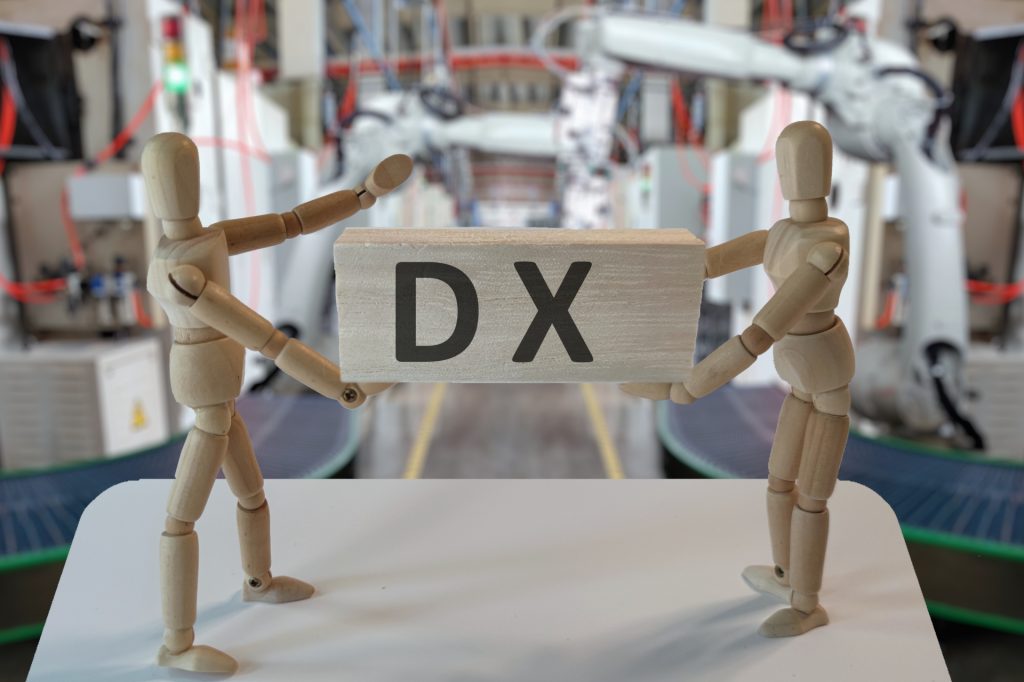
生産管理は業務範囲が広く、様々な部門と連携しながら製造現場全体を管理する重要な役割を担うため、DXを推進することが非常に重要です。
本章では、生産管理業務に焦点を当ててDX事例をご紹介します。
事例①需要予測のできるAIを活用した事例
某大手食品メーカーでは、AI需要予測システムを導入しています。
以前は2,000種類を超える商品の需要予測を、わずか7名の担当者が経験や過去実績を元に需要予測を行っていました。
所要時間や結果のばらつきに課題を感じ、AI需要予測システムを導入したところ、以下のような効果がありました。
- 予測精度の向上
- 需要予測に関する時間の大幅な短縮
- 需要予測業務に関する属人化の解消
事例②生産・要員計画にAIを活用した事例
某大手食品メーカでは生産・要因計画にAIを活用したことで、以下のような効果がありました。
- 生産計画に掛かる時間を10分の1に短縮
- 熟練者の考慮する制約をデータ化し属人化解消
- 一カ所のみならず全国の工場で活用し全社的な生産性向上を目指せる
事例③異常予兆検知にAIを活用した事例
某大手化学品メーカーでは、製造過程での異常を正確に検知するために、AIが搭載された異常予兆検知システムを導入したところ、以下のような効果がありました。
- AIが正常な状態のデータを蓄積し、微小な異常を感知できる
- 経験の浅いオペレーターでも正確に設備監視ができる
- 熟練者のノウハウをAIを通じてデータベース化できる
自社の課題に合った生産管理を行ったうえでDX推進するのが重要
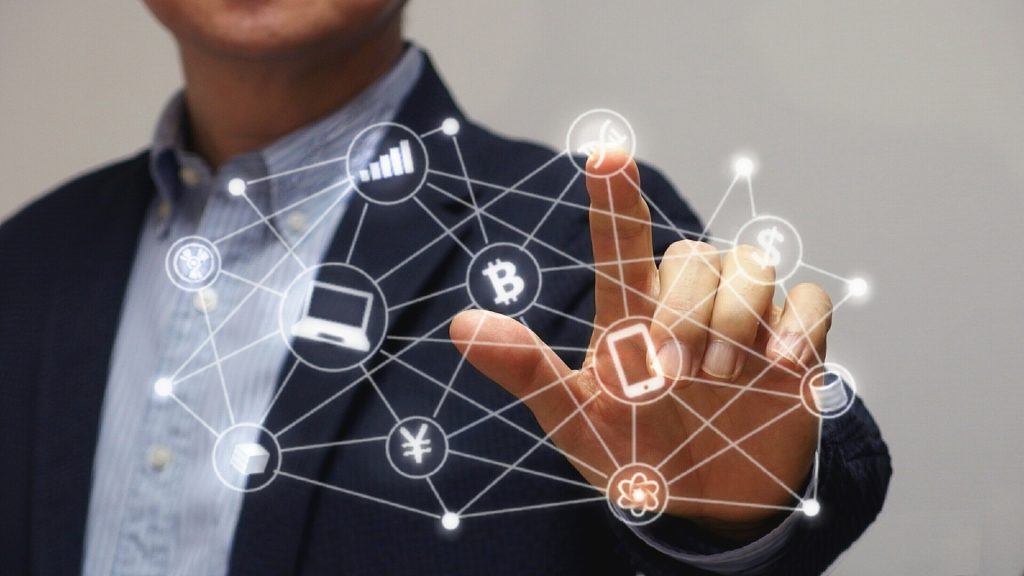
本記事では、生産管理の基本的な仕事内容や付随する知識をご紹介しながら、生産方式別の生産管理の特徴や実際のDX事例について解説してきました。
従来の生産管理では、経験やスキルに基づいた予測が必要であり、業務が属人化しやすいという課題がありました。
生産管理システムやAIを使った予測や検査を行うことで、より正確で迅速な管理が可能です。
当社では、工程管理・購買管理・在庫管理などさまざまなシステムを連携できる「rBOM」をご提供しております。
以下のホワイトペーパーでは、生産管理システム選定と導入のポイントもご紹介しているため、ぜひご覧ください。
おすすめのお役立ち資料はこちら↓
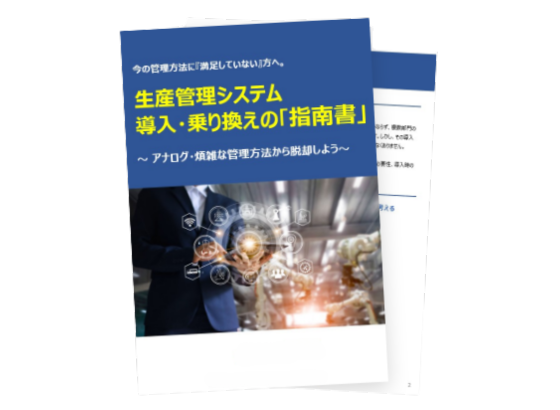
今の生産管理方法に不満がある、という方へ。
生産管理システム 導入・乗り換えの「指南書」
